Johnson Matthey and bp technology chosen for the world’s largest Fischer Tropsch SAF production plant
Johnson Matthey and bp technology chosen for the world’s largest Fischer Tropsch SAF production plant
10 April 2024
DG Fuels has chosen Johnson Matthey and bp’s co-developed Fischer Tropsch (FT) CANS™ technology for its first sustainable aviation fuel (SAF) plant.
Located in Louisiana, USA, it would be the largest announced FT SAF production facility in the world, with a planned capacity of 13,000 barrels per day – capable, after blending to 50%, of producing enough SAF for more than 30,000 transatlantic flights annually.
DG Fuels has already secured offtake agreements with Delta Air Lines and Air France-KLM, and has a strategic partnership with Airbus to scale up the use of SAF globally.
Signed at the end of March, this is the tenth sustainable technologies project win in Catalyst Technologies since April 2022, delivering on our strategic milestone for large scale project wins.
Johnson Matthey (JM), a global leader in sustainable technologies, today announced that DG Fuels has selected its award-winning Fischer Tropsch (FT) CANS™ technology – co-developed with bp – for DG Fuels’ first sustainable aviation fuel (SAF) plant in St. James Parish, Louisiana. The plant would be the largest deployment of FT CANS to date, seven times larger than any previously announced project using this technology.
DG Fuels is an emerging leader in renewable hydrogen and biogenic based, synthetic SAF and diesel fuel. The proposed $4 billion DG Fuels plant is planned to produce 600,000 metric tons (MT) of SAF per year when fully operational and would be the largest announced SAF production plant using a non-HEFA[1] route. DG Fuels is planning 10 more SAF production plants across the United States. These would be modelled on the Louisiana plant with JM and bp as the partners of choice for these facilities.
The fuel at the Louisiana plant is expected to be produced from waste biomass. DG Fuels is projected to purchase around $120 million of sugar cane waste annually, a third of which is planned to be purchased from St. James Parish farmers. JM and bp’s FT CANS technology converts the synthesis gas derived from this biomass to synthetic crude, which is then further processed to produce the synthetic kerosene that is then blended with conventional jet fuel to produce SAF.
Current international certification for this SAF requires a blend of up to 50% with fossil kerosene to create “drop-in SAF”. Based on a typical widebody aircraft fuel consumption rate travelling the distance from London to New York, the plant's planned SAF production capacity, after blending, is equivalent to the fuel required for over 30,000 transatlantic flights annually, equivalent to more than 3% of annual traffic flying on that route currently.
The plant is expected to start production by 2028. DG Fuels has already secured offtake agreements with major airlines, including multi-year deals with both Air France-KLM and Delta Air Lines. DG Fuels also has a strategic partnership with Airbus to help make SAF available at scale around the world.
Maurits van Tol, Chief Executive for Catalyst Technologies at Johnson Matthey, said: “The size of this project is truly exciting and would help take the industry closer to wide-scale use of SAF. DG Fuels has ambitious plans and the fact it has secured agreements with major airlines demonstrates there is appetite in the market. Our FT CANS technology enables cost-effective deployment across a wide range of project sizes. We look forward to working with DG Fuels as a long-term partner for SAF production.”
Noemie Turner, VP Technology Development & Commercialisation at bp, said: “The aviation industry is looking to greatly increase its use of SAF, and we’re proud that DG Fuels has selected our technology to be at the heart of their ambitious plans for large scale SAF production. Our FT CANS technology solution brings together decades of science and engineering expertise from bp and JM, and this project shows its competitiveness across the range of production scales and feedstock sources the industry needs. We’re excited to see the relationship with DG Fuels grow, and we look forward to seeing this project come to fruition.”
Christopher J. Chaput, President of DG Fuels, said: “We are extremely excited to be moving forward with Johnson Matthey to execute our unique strategy of high carbon conversion. With this technology, we will create a product that is responsibly made and can be immediately substituted for conventional aviation fuel with no engine adaptations. This partnership is a significant boost to help the aviation industry reach its climate goals.”
Michael Darcy, CEO of DG Fuels, said: “Using Johnson Matthey and bp’s co-developed Fischer Tropsch (FT) CANS™ technology allows DG Fuels to scale SAF at high volume production and competitive prices for the first time ever. This innovation will take DG Fuels' SAF from the sugar cane fields of Louisiana to cleaner skies all across the world.”
For media enquiries contact:
Johnson Matthey Press Office:Email: jmpr@matthey.com
Telephone: +44 207 269 8001
bp Press Office:
Email: bppress@bp.com
Telephone: +44(0)7831 095541
DG Fuels Press Office:
Email: Katie McKeogh – mckeogh@tegpr.com
Telephone: 504-442-4074
[1] Most of the SAF supplied today is derived using the Hydrotreated esters and fatty acids (HEFA) pathway. The primary feedstocks for this conversion pathway include waste fats, oils, and greases. While HEFA synthetic paraffinic kerosene (SPK) is currently the main commercial pathway being used at scale to produce SAF, feedstocks are limited so we expect to see need for commercial large-scale sustainable feedstock mobilisation. (Good discussion at: How all sustainable aviation fuel (SAF) feedstocks and production technologies can play a role in decarbonising aviation | News and views | Air bp) (accessed online 2 April 2024).
More about our Fischer Tropsch technology
Explore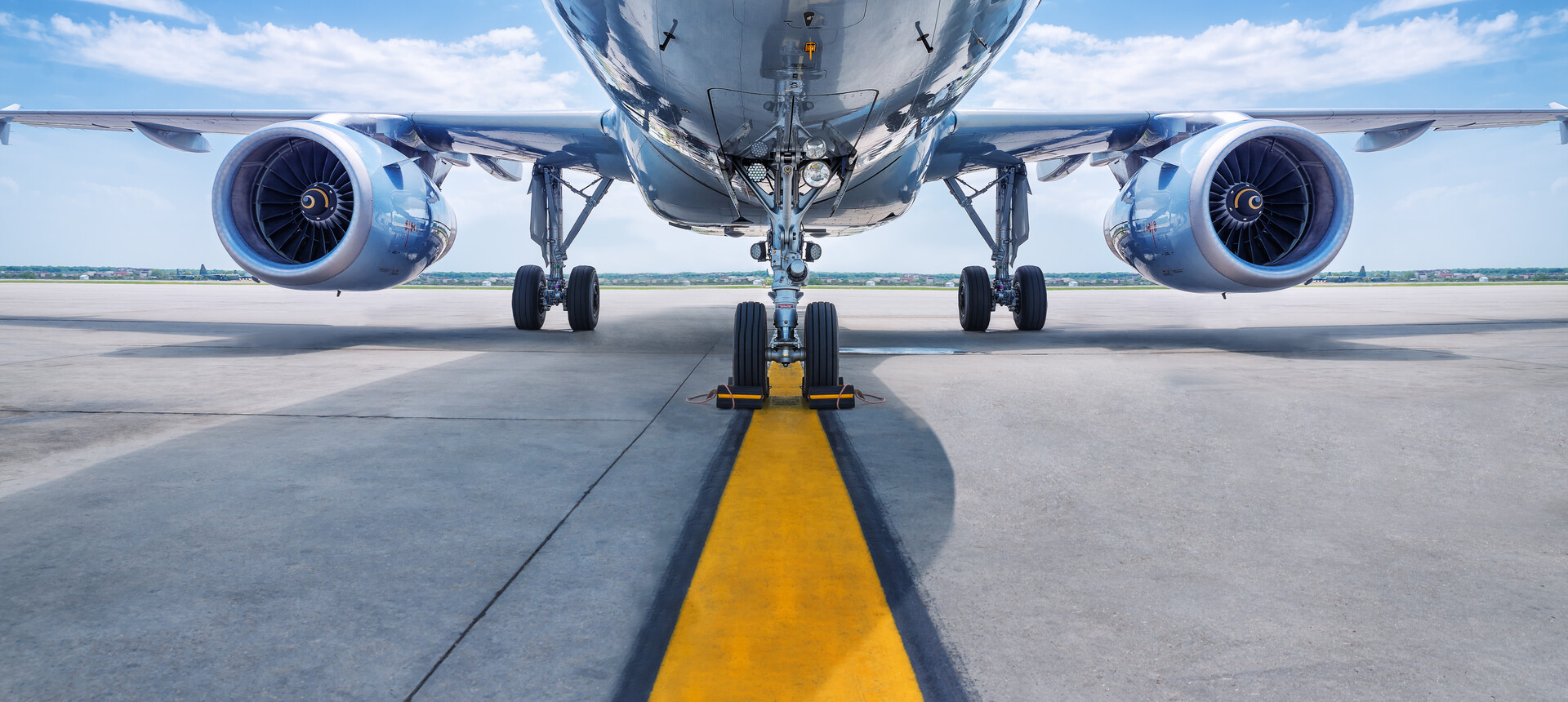
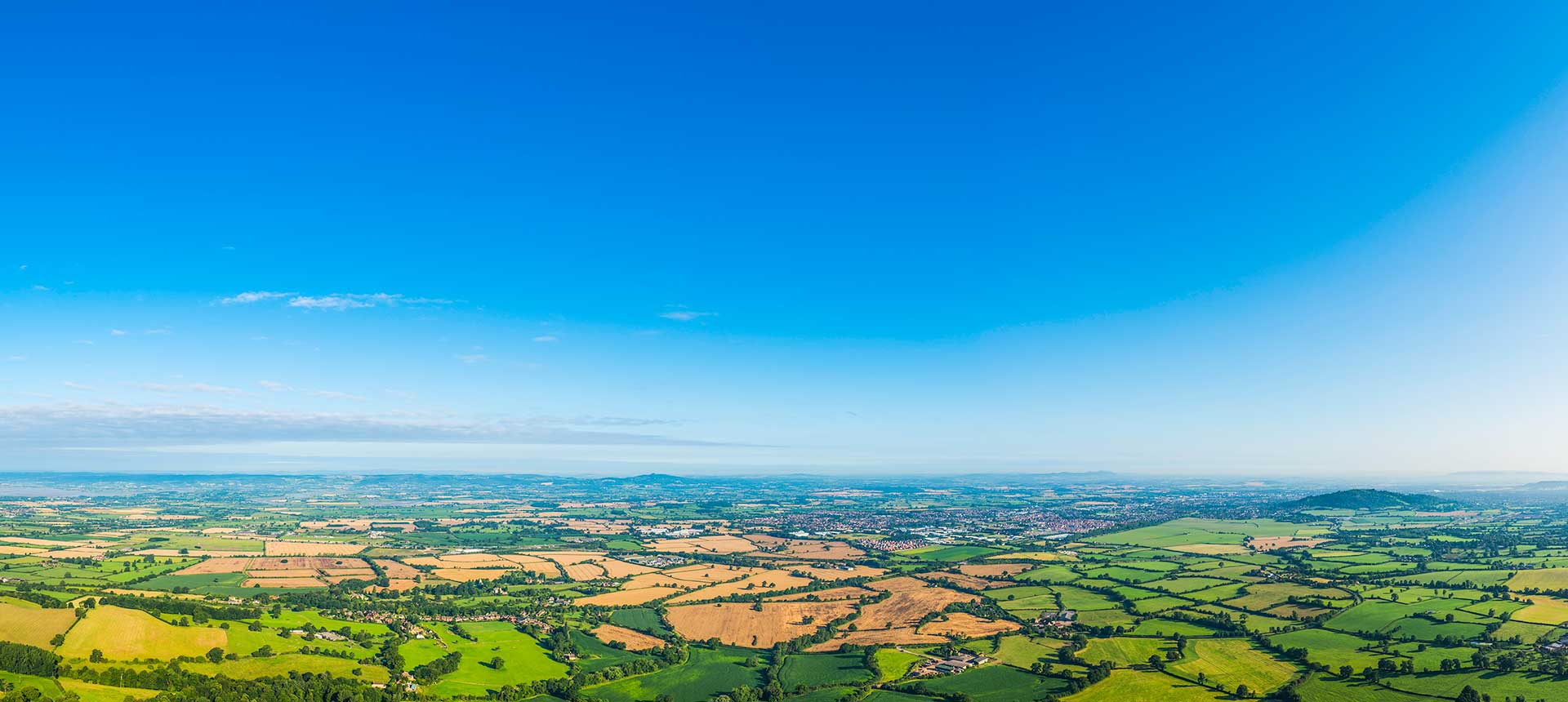