CO oxidation FCC additives
Combustion promoters are required to ensure smooth regenerator operation, control of afterburning and reduction of carbon monoxide (CO) emissions.
Afterburning occurs when carbon monoxide reacts exothermically with oxygen in the regenerator dilute phase to form carbon dioxide. Because of the lack of catalyst available to absorb the heat of CO combustion, the dilute phase experiences a large increase in temperature—a common constraint in FCC unit operations. As a result, high afterburn limits throughput and ability to run heavier feed by forcing refiners to operate at lower bed temperatures.
A CO promoter is used to accelerate this reaction in the regenerator dense phase (catalyst bed) where there is more catalyst available to absorb the heat of reaction.
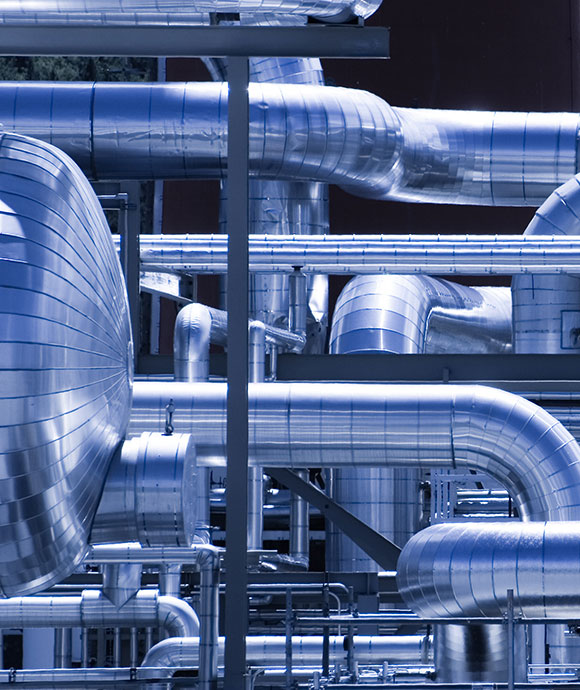
Enhancing CO oxidation with FCC additives
Promoters employ platinum group metals (PGMs), supported on a high surface area alumina, to ensure a high metal dispersion. A high metal dispersion provides a high catalyst activity, allowing the optimum amount of precious metal to be used.
In addition, high metal dispersion provides resistance to catalyst deactivation via sintering, therefore allowing for less additive to be used. By leveraging Johnson Matthey’s deep understanding of PGMs, the amount of metal used is minimised while achieving outstanding catalyst performance.
All Johnson Matthey promoters have an attrition resistance, bulk density, and particle size distribution fully compatible with the circulating catalyst inventory and are available for delivery in a variety of packaging options.
Johnson Matthey offers state-of-the-art additive addition systems that enable refiners to accurately inject small quantities of additive throughout the day, optimising both performance and cost.
Platinum-based promoters for CO oxidation
Platinum-based promoters are effective at converting CO to CO2 in the dense phase, playing a critical role in CO oxidation and controlling afterburn.
Johnson Matthey offers several platinum-based promoters. The lower activity grades (COPTM-250 and 375) are often used in FCC units with large regenerators to ensure high amounts of particles available for contact within the dense bed.
These products have less platinum per particle and are used with a higher addition rate to ensure the platinum is evenly distributed in the regenerator. The higher activity grades (COP-550 and 850) provide a good balance of additive activity and cost and are used to reduce daily additions.
Non-platinum promoters for CO oxidation and reduced NOx emissions
While platinum-based promoters offer excellent afterburn control, they also tend to increase regenerator NOx emissions. Non-platinum promoters have been developed for refiners who need to control afterburn and CO oxidation with minimum NOx emissions. JM’s non-platinum promoters have equivalent performance to platinum-based promoters, effectively managing both afterburn and CO with reduced NOx emissions.
COP-NPTM is an EPA approved non-platinum promoter used by many FCC units worldwide. It controls afterburn while reducing NOx emissions by over 70% compared to platinum-based promoters.
COP-NP HD is a new product that employs advanced technology to improve metal dispersion and metal-support interaction. This new product controls afterburn with a lower daily cost for the end user.
Read our article Optimising FCC economics against changing market dynamics