Sulphur oxide reduction FCC additives
Government agencies worldwide are adopting ever more stringent legislation regulating the levels of sulphur oxide (SOx) emissions from oil refineries. While FCC feedstock desulphurisation and flue gas scrubbing are both proven methods for FCC flue gas SOx emission control, many refiners find that the use of an in-situ SOx reduction FCC additive is the most cost-effective means of meeting these regulatory requirements.
SOx reduction additives are added directly to the FCC catalyst inventory where they adsorb sulphur oxides in the regenerator, releasing the sulphur as hydrogen sulphide in the riser. Hydrogen sulphide is routinely processed in the refinery sulphur recovery unit (SRU) where it is then converted to elemental sulphur. The incremental hydrogen sulphide production is relatively low and can usually be handled by existing sulphur recovery facilities.
Read our article Emission challenges in partial burn FCC operation
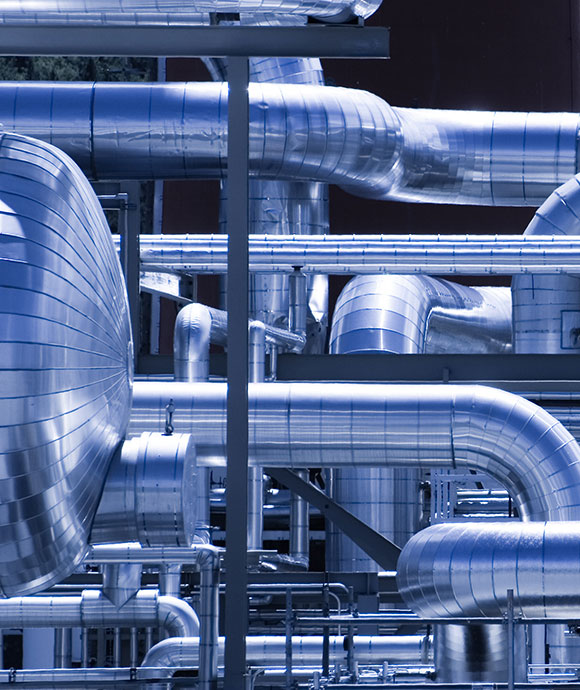
Decreasing the cost of SOx reduction
Johnson Matthey’s SUPER SOXGETTERTM and LO-SOXTMPB families of SOx reduction additives have been developed to decrease the cost of removing SOx from the FCC flue gas in full burn, partial burn and two-stage regenerators.
-
These additives are based upon hydrotalcite-like compounds that maximise the accessibility of sulphur-containing regenerator gases to the reactive magnesium containing sorbate phase in the additive.
-
The high magnesium content of these additives allows them to outperform products based on all other sorbate technologies and have been proven commercially to be the most effective additives in the marketplace.
-
Our SOx reduction additives can easily achieve and maintain SOx reduction levels of over 95% with no negative impact on unit operation yields, or process equipment.
SUPER SOXGETTER X2 is the newest Johnson Matthey’s SOx reduction additive.
-
SUPER SOXGETTER X2 additive achieves greater SOx reduction with less additive, resulting in lower operating costs and expanded FCC unit operating window.
Download our case study on using SOx reduction additives to reduce FCC OPEX