Formaldehyde plant range
The latest FORMOX™ design is a step further in the evolution of our plant technology. The foundation of our offering is our 3 well-proven plant sizes which can be set up in various ways to meet customer requirements and local conditions, e.g. twin reactors, turbocharger, UFC, superheated steam. The latest design has also been optimised to cut capital costs.
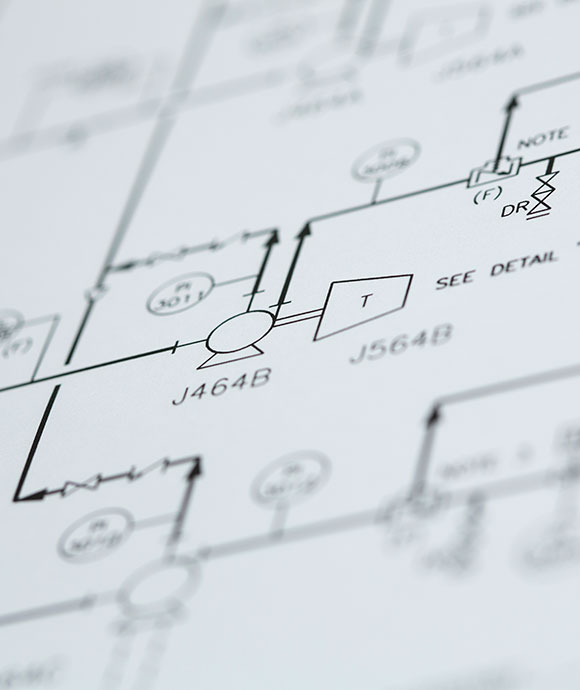
Our standard formaldehyde plants
Our range of standard plants now covers a capacity range extending from 70 MTPD to nearly 840 MTPD in one production unit. The single line configuration ranges from 70 to 418 MTPD capacity. For higher capacity the FORMOX twin-stream (FT) range has two reactor streams each feeding a common absorber and ECS. The largest can produce up to 836 MTPD.
For plants with the twin reactor configuration, both lines can be installed from the start. Or by choosing the expandable versions (FE2 or FE3), you can postpone your investment in the second line. This expandable scheme has been used many times and is a good solution for a formaldehyde producer who sees good growth potential but wishes to keep the initial investment to a minimum.
Moreover, when set up for UFC production, a FORMOX plant can produce either UFC (up to 85%) or formaldehyde (up to 55%) in campaigns.
Standard options
Our philosophy is to see that you get the most formaldehyde out of the least methanol at the lowest possible cost, and with sustainable impact on the environment. This is why all plants are equipped with an emission control system which is designed to meet all the prevailing emissions legislations globally. Since specific needs and wishes vary considerably from producer to producer, we aim for the greatest possible flexibility. That's why we have a wide range of standard options, including:
Low power
- The use of a turbocharger for supplying the process with fresh air at elevated pressure is a technological breakthrough that saves approximately one third of the power consumption of the plant. Please see the FORMOX formaldehyde process for more details about the turbocharger concept.
- Superheating of high-pressure steam in the ECS. For use in a steam turbine either inside battery limit (driving a fan on the FORMOX process) or external electrical power production. Depending on local conditions, alternatives can be considered.
UFC/formaldehyde
Plant design that is fully flexible between 55% formaldehyde and UFC85.
Alternative feedstock
FORMOX plants can use bio/green methanol and methanol combined with various recycled methanol streams, as well as standard grade methanol. This can significantly reduce the carbon footprint and make your production more sustainable. The FORMOX plant design can also be adjusted with technology that enables the use of methylal or methylal/methanol mixtures as feedstock.
Low methanol
By optimising the loading profile extremely low residual methanol in the product is possible.
Investment and scope of supply
All investment packages include the right to use and operate the FORMOX process, but vary in the level of engineering support and the extent of the equipment supply. For instance we can offer full equipment supply, which includes most of the IBL equipment required to erect the plant. In addition to the process engineering package, we can provide a detailed engineering package containing the detailed engineering for piping as well as electrical and instrument design required to construct the plant. At the other end of the scale we can offer a basic engineering together with an engineering sample package and only key equipment.
During the erection, commissioning and start-up of the plant, we provide advisers on site to guide the work and ensure successful completion of the project. For all new FORMOX plants, JM-LEVO Formaldehyde Portal is included with the first catalyst delivery, in order to enable optimization of the plant operation from day one.
Java method "com.sun.proxy.$Proxy917.getLatestArticle(long)" threw an exception when invoked on com.sun.proxy.$Proxy917 object "com.liferay.journal.service.impl.JournalArticleLocalServiceImpl@3e549bca"; see cause exception in the Java stack trace. ---- FTL stack trace ("~" means nesting-related): - Failed at: #assign article = JournalArticleLocal... [in template "161555#161602#ACCORDION" at line 15, column 13] ----
1<#assign JournalArticleLocalService = serviceLocator.findService("com.liferay.journal.service.JournalArticleLocalService")>
2
3<div class="container jmaccrdn">
4<#if Sections?? && (Sections.getSiblings())?? && Sections.getSiblings()?has_content>
5 <#if (Title.getData())?? && Title.getData()?has_content>
6 <h2 class="jmaccrdn__heading">
7 ${Title.getData()}
8 </h2>
9 </#if>
10 <div class="accordion" id="accordion">
11 <#list Sections.getSiblings() as cur_Sections>
12 <#assign
13 webContentData = jsonFactoryUtil.createJSONObject(cur_Sections.getData())
14 />
15 <#assign
16 article = JournalArticleLocalService.getLatestArticle(getterUtil.getLong(webContentData.classPK, 0))
17 />
18 <@liferay_journal["journal-article"]
19 articleId = article.getArticleId()
20 ddmTemplateKey = "ACCORDION-SECTION"
21 groupId = article.getGroupId()
22 />
23 </#list>
24 </div>
25</#if>
26</div>
27
28<style>
29
30@media (min-width: 320px) and (max-width: 539px) {
31 .jmaccrdn .jmaccrdn__heading {
32 font-size: 24px;
33 padding-left: 20px !important;
34 padding-bottom: 7px !important;
35 padding-top:0px !important;
36 }
37}
38@media (min-width: 540px) and (max-width: 834px) {
39 .jmaccrdn .jmaccrdn__heading {
40 padding-bottom: 40px !important;
41 padding-top:0px !important;
42 }
43}
44</style>