Turbocharger and steam utilisation process
In most high power cost situations, a turbocharger is the preferred design with short payback on the extra investment.
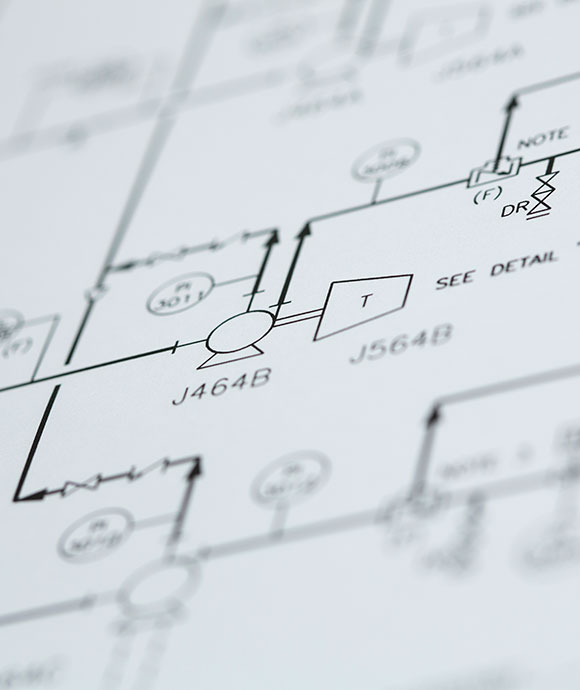
Pressurisation with turbocharger
In most high power cost situations, a turbocharger is the preferred design with short payback on the extra investment. The turbocharger recovers energy from the stack gas, reducing power consumption. As the exhaust turbine is directly coupled to a compressor, the turbocharger takes the place of the pressurisation blower. An additional benefit is that most of the thermal energy is recovered as steam and remains available for heat recovery or is taken to a turbine. In the longer term, the turbocharger offers the possibility of economical operation at even higher pressures and hence even higher productivity or optimised performance.
Steam utilisation
The first point to consider is whether the steam can be exported; as the condensing energy is used, the value is generally higher. For many sites steam is a cost for condensing to recover BFW. Yet other sites may use steam only intermittently (for example, resin producers), while the rest is blown off or condensed. In other words, no single solution will fit all types of plant; what best suits your site depends on the site steam balance and site requirements in terms of steam, pressure and temperature.
Assuming the steam cannot be exported, the basic options are:
- use the steam directly, to drive the blower
- or indirectly by using the steam to drive a generator and generate electricity.
In both cases superheating the steam will give a better result. And there are also different types of turbines available:
- Single-stage steam turbines
- Multi-stage steam turbines.
In addition, the unit can either be a "pass-out" turbine (designed to pass out steam at a lower pressure) or a condensing turbine. And the condensation can be either at atmospheric pressure or under vacuum (provided cooling water is available at a low enough temperature). Given all these permutations and combinations, it is difficult to be specific. In the examples quoted in the table, all plants are fitted with a methanol prevaporizer and a steam superheater; the inlet steam conditions are 21 bar g and 350°C.
In general terms, around 50 to 60% of the energy can be saved with a single turbine - considerably more with a multistage turbine - but at a very much higher cost. The most economical option is direct drive from a single turbine.