Solvent purification
For more than 20 years, many customers worldwide have successfully used HTC™ in solvents, fuels, white oils, waxes and other similar applications for de-aromatisation, desulphurisation and removal of undesirable and/or toxic aromatic and olefinic species from solvent streams using hydrogenation.
The catalysts are characterised by a highly dispersed active metal phase and an open pore structure. High metal dispersion is equivalent to small crystallite size and provides a high metal surface area per gram of metal. Catalyst activity is directly linked to metal surface area. Large pores are important to make the metal surface area accessible and minimise diffusion.
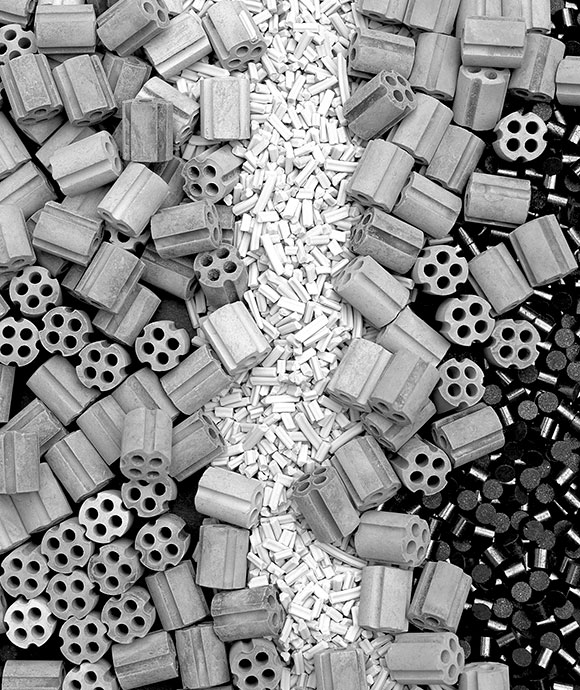
The above mentioned features result in high activity, high selectivity and poison resistance, which is nowadays required to turn difficult feeds into low-aromatic and low-sulphur products. The high physical strength and low attrition index ensures a trouble-free operation, even at longer lifetimes, and easy unloading at end of run.
HTC catalysts have been used to produce a wide range of solvents from a variety of hydrocarbon feedstocks including gasoline, kerosene and diesel type fractions. The catalysts commonly reduce aromatic contents from several wt% to less than 50ppm, with tighter specifications achievable as required. These catalysts have also been proven in the manufacture of high quality medicinal white oils, highlighting the unique characteristics of this catalyst range.
Similarly, olefinic solvents can be produced with bromine indices below 10 mg Br2/100g. We have experience of a wide range of feedstocks, both light materials such as hexane or heavier species such as PAO (poly-alpha olefins). In response to market demands for higher activity and improved sulphur tolerance Johnson Matthey has expanded its HTC range with HTC NI 700 RP 1.2 and HTC NI 900 RP 1.2. The newest products complement the portfolio with a high activity long life solution.
In some special applications, supported precious metal catalysts provide the highest performance. Please, contact us to discuss your requirements.
Catalyst
|
HTC NI 400 RP1.2 |
HTC NI 500 RP 1.2 |
HTC NI 600 RP 1.2 |
HTC NI 700 RP 1.2 |
HTC NI 900 RP 1.2 |
Nickel content (wt%) | 17 | 21 | 27 | 32 | 39 |