Our world is changing and the way we produce power, design backup power systems, run our industries, travel, and move goods is evolving along more sustainable pathways. This drive for greater sustainability requires both natural and green fuels to be used in the most efficient, effective, and environmentally friendly manner and SOFC is one such technology that efficiently converts fuels into electricity and heat.
Following a long history of developing materials and catalysts, we now have a portfolio of SOFC technologies for purification, reforming, (partial) oxidation, and trapping for a wide range of fuel feeds including biogas, renewable natural gas, natural gas, ammonia, hydrogen, and fuel blends.
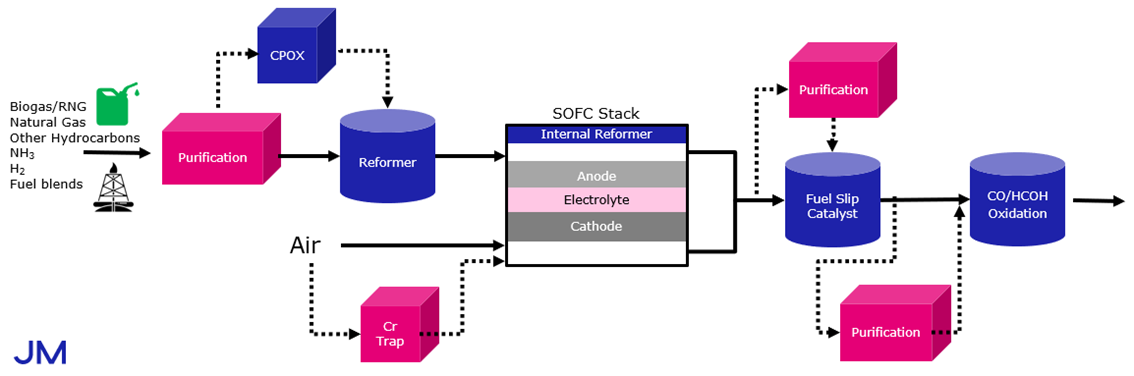
Component |
Purpose |
Purification |
To remove sulphur species present in certain fuel feeds like natural gas. |
CPOX |
Partial oxidation catalyst that can generate syngas. |
Reformer |
To reform higher hydrocarbons and deliver the correct ratio of CH4/H2/CO to the internal reformer/stack. |
Internal reformer |
To reform the remaining methane in the feed gas utilising the heat from the stack to drive the endothermic steam reforming reaction. |
Fuel slip catalysts |
To oxidise residual CH4/CO/H2 from the anode off-gas to CO2 and H2O to comply with emission limits. |
CO/HCOH |
To oxidise CO and Formaldehyde to CO2 and H2O. |
Chromium trap |
To capture Cr vapour generated from the system alloys that can readily poison the stack. |
Our product offering
Technology options include both base metal and precious metal catalyst solutions available as coated components e.g., on traditional monoliths structures, or on more advanced substrates, such as heat exchangers, flat or semi-flat plates, and other structures using manufacturing processes that scale.
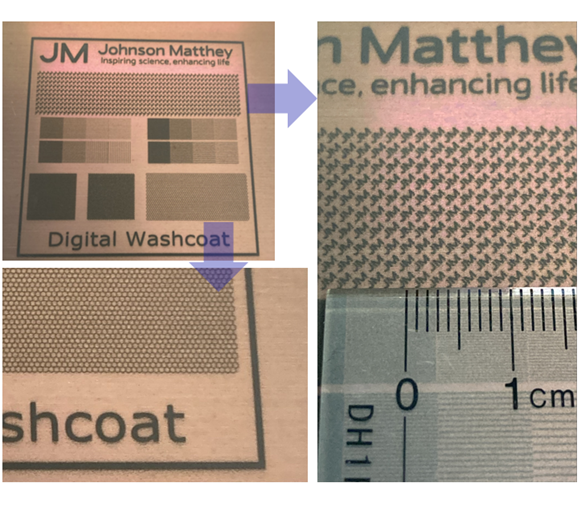
Analytical and failure mode testing capabilities
We also have world class analytical facilities to test the performance of our SOFC components and analyse fresh and aged products to understand aging mechanisms and failure modes. For example, we not only have Cr trapping catalysts that can operate in the temperature range of ~300-800°C, we have in-house test capabilities to evaluate Cr traps under various conditions, a rare capability, and we continue to innovate in this space.
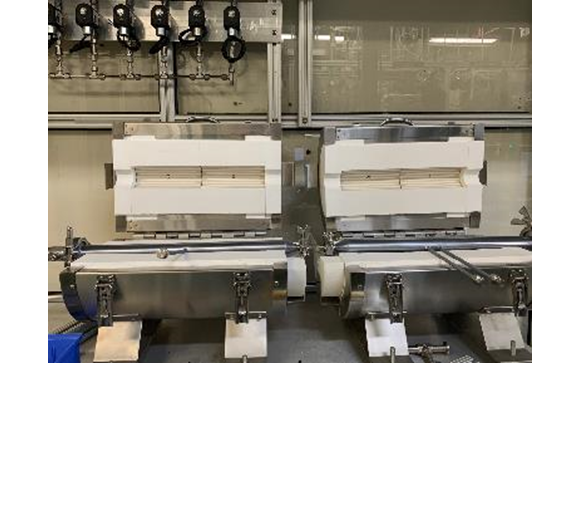
If you are designing and building SOFC systems, leverage the product development, process development, and industrialisation teams at Johnson Matthey to deliver the most value from your system and secure a reliable supply chain to mass produce components.