Metal brazing – tips and advice
What is brazing?
About brazing
Brazing is a versatile joining process. It is used to join most metals and alloys commonly used in engineering. It is a thermal joining process in which a molten brazing filler metal is drawn into a capillary gap between the metals being joined.
Brazing filler metals have a melting point above 450˚C but below the melting point of the metals being joined.
Soldering differs from brazing in that it takes place at temperatures below 450˚C, although both processes occur below the melting point of the metals being joined.
The properties of a successfully brazed joint
- Strong and ductile - well made brazed joints can be at least as strong as the parent metals being joined and will withstand demanding service conditions.
- Leak tight - brazing produces leak tight joints widely used on liquid and gas pipe-work installations.
- Electrical conductivity - brazed joints offer good electrical conductivity and are used in applications where this property is important.
- Joint appearance - brazed joints have smooth, neat fillets.
Terms associated with the brazing process and brazing filler metals
Brazing alloy / filler metal
A filler metal which melts above 450˚C but below the metals being joined.
Flux
A chemical compound applied to the parent metals to protect them from oxide formation during heating and to promote flow and wetting of the brazing filler metal.
Parent metals
The materials to be joined by brazing.
Wetting
When molten brazing alloy flows over and adheres to the parent metals.
Joint gaps
The gap between the parent metals to be joined by the brazing filler metal.
Capillary attraction
The force that draws a molten brazing alloy into the joint gap.
Solidus
The highest temperature at which a filler metal is completely solid.
Liquidus
The lowest temperature at which a filler metal is completely liquid.
Melting range
The temperature range over which the filler metal melts.
Eutectic
An alloy (filler metal) with a single melting point rather than a melting range is known as a eutectic alloy.
Six steps of successful brazing
1. Joint design
Brazed joints should always have a capillary gap into which the molten filler metal can flow. Joint strength will vary with the joint gap and the degree of overlap between parent metals. The optimum joint gap at brazing temperature is shown in the table of physical properties for each product.
Different expansion rates of the parent metals will affect the joint gap at brazing temperature. For lap joints use an overlap length of 3 to 4 times the thickness of the thinnest parent metal part in the joint.
For tubular parts of sizes up to 25mm in diameter the joint overlap should be equal to one tube diameter.
2. Choice of brazing filler metal alloy
Alloys should be chosen on their suitability for a particular application. Consider the component design, the parent metals, the brazing process and cost.
The brazing filler metals that are easiest to use are the high silver, free flowing filler metals with low melting ranges. Filler metal alloys with higher brazing temperatures and longer melting ranges are more difficult to use.
3. Pre-cleaning
The components to be joined should be free from grease and any surface oxide prior to brazing to promote good bonding. Grease and oil are best removed using a degreasing solvent. Hot, soapy water may also be effective.
4. Fluxing the joint
The choice of flux is as important as the choice of filler metal. The working range of the flux must be compatible with the brazing temperature and the parent metals. Ideally flux should be applied to both components before assembly and prior to heating.
The flux melts and become active below the melting point of the brazing alloy. It must stay active right through the brazing cycle removing the oxides formed on the parent metals. If the flux residues appear blackened and glassy the flux has probably been exhausted during heating.
This could be because either insufficient flux has been used or the components have been overheated. Alternatively, a flux with greater time and temperature stability should be used.
5. Heating the joint and applying the filler metal
Several heating methods are used for silver brazing in air. They include hand torch, fixed burner, induction and resistance heating. In addition, for torch or fixed burners different fuel gas combinations are available from oxy-acetylene, oxy-propane, through to air / natural gas.
For brazing it is essential that the parent metals are heated evenly to the correct temperature. The flux should be clear and flow over the joint area.
When brazing copper with an alloy from the SIL-FOS™ and COPPER-FLO™ range the metal should be a dull cherry red indicating the correct temperature has been reached.
Brazing rod, strip or wire should then be touched onto the joint mouth when brazing temperature is reached.
Free flowing filler metal alloys will flow into and around the joint by capillary attraction. A sluggish flowing filler metal alloy should be applied along the entire joint, building up a fillet. Molten brazing filler metal always flows to the hottest part of the joint.
Heating should continue as the filler metal flows into the joint. For torch brazing indirect heating should be used. Once brazing is complete heating should be discontinued.
6. Removing the flux residues after brazing
When the alloy has solidified the joint can be water quenched to help remove flux residues. During cooling care must be taken not to damage the component or cause cracking due to thermal shock.
It is important to remove flux residues after brazing.
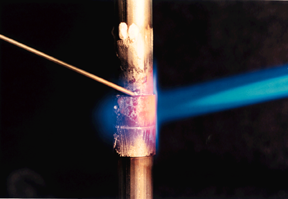
Brazing techniques
How to use a brazing flux
Why use a flux?
A molten brazing filler metal will only wet and flow over a parent metal if both are substantially free of surface oxide. Simply removing surface oxide before brazing is not effective, since a new oxide layer is rapidly formed on heating. To achieve an oxide free surface, it is necessary either to:
1. Remove oxide as it is formed by the use of a suitable brazing flux.
2. Prevent oxidation during brazing by heating in a protective atmosphere or vacuum.
3. Use a self-fluxing brazing alloy - only applicable when brazing copper to copper.
Brazing fluxes are only designed to remove oxide films. Where other contaminants such as oil, paint and lacquer are present these should be removed before brazing, using either mechanical or chemical methods.
How to use a brazing flux
It is recommended that flux should be applied as a paste to the parts to be joined.
Powders can be made into pastes by stirring in water until the mixture has the consistency of thick cream. A few drops of liquid detergent added to the mixture will often improve the wetting of flux onto clean parent metals.
The flux should be applied to both joint surfaces before assembly. Application of flux after assembly places great demands on the fluidity of the molten flux and its ability to penetrate capillary joints. Flux may be applied in the following ways:
1. Brushing is an effective method of applying a thin film of paste to the joint itself and to surrounding component surfaces.
2. Brazing flux may be applied by dipping one or more components of an assembly into a container of flux. This is most effective with a paste of a thin consistency.
3. Automatic application of flux is possible and can be used for mass production; contact us for more information.
4. Hot rodding is a technique in which a warm brazing rod is dipped into flux powder and the flux adhering to the rod is transferred to the joint area. This is an effective fluxing method but difficult to achieve good penetration of capillary joints. A refinement on this technique is the use of flux coated brazing rods.
Factors which affect how a flux works
The ability of any flux to perform satisfactorily during a brazing operation will depend on the brazing temperature and time, the parent metals, and the volume of flux applied.
Temperature
To be effective the flux must be both molten and active before the brazing alloy melts, and it must remain active until the brazing alloy flows through the joint and solidifies on cooling. It is good practice to select a flux which is active at least 50oC below the solidus of the brazing alloy and which is still active at a temperature at least 50°C above the liquidus of the brazing alloy. This will ensure that the flux is effective during the brazing operation.
Time
The flux should remove the oxides on the component and must continue to remove fresh oxide until the completion of the brazing cycle. There is a limit to the amount of oxide that the flux can dissolve, although the longer the heating cycle the more likely it is that the flux will become exhausted.
With long heating cycles the use of flux with a higher working range would be recommended. For short rapid heating cycles, it may be possible to use a flux above its recommended maximum working temperature.
Parent metals
Our fluxes are suitable for use on copper, brass, mild steel and most other common engineering materials. Special purpose fluxes exist for aluminium bronze, stainless steel, tungsten, molybdenum and tungsten carbide. Silver brazing fluxes are not effective on aluminium, magnesium, titanium or their alloys.
How to use a copper-phosphorus brazing rod
- When joining copper to copper no flux is required. Heat the inserted component first then heat evenly.
- Transfer the flame to heat all around the base of the socket.
- When the components are a dull cherry red colour touch the rod onto the joint.
- Use the heat from the torch to pull the filler metal into and around the joint. Cool in air after brazing.
How to use a flux coated rod
Flux coated rods combine flux and brazing filler metal in a single convenient form. They are suitable for use on joints where there is a limited gap for the filler metal.
- As the joint is heated the flux coated rod should be touched or wiped onto the joint area. This will apply some flux and protect the component from oxidation as the joint approaches brazing temperature.
- At brazing temperature, the now bare end of the rod should again be touched onto the joint and held in position if the alloy begins to flow.
- Turning the rod between the fingers will ensure that the flux melts off the rod and onto the component evenly.
- Avoid heating the rod directly with the torch flame as this will melt the flux off the rod leaving no flux available for the next joint.
- Heat evenly to brazing temperature. Feed the bare end of the flux coated rod into the joint whilst heating the component evenly.
- Flux residues must be completely removed by soaking in warm water for about 30 minutes.
How to use brazing and soldering paste
The use of paste requires different techniques and general practices to those employed for other forms of brazing or soldering consumables. The basic principles always apply.
Location of paste deposits
Whilst no particular joint design is excluded from brazing or soldering with paste, the suitability of a component is dependent on there being a place to deposit the required amount of paste. Ideally the component should have a shoulder or ledge on which the paste can be adequately supported.
Components should be assembled and the paste applied as near to the mouth of the joint as possible. Avoid placing paste inside the joint as it may not burn off completely, restricting the flow of the flux and alloy.
If the component does not have a convenient shoulder or ledge then the paste should be applied above the joint. Any movement of the paste during heating can be controlled to direct the flux and alloy flow towards the mouth of the joint. In this case a flux binder system with minimal slump characteristics is recommended.
Dispensing of paste onto components
A major advantage of using a paste is that it can be dispensed in accurate and controlled volumes, ensuring that a particular joint receives the same amount of paste on each application.
Paste is often supplied in cartridges, which can be fitted to accurate air operated dispensing machines. Where larger volumes of paste are required a reservoir connected to a paste gun can be used. Paste can be supplied in hand cartridges for manual dispensing although this reduces the close control over paste volumes achieved with even the most basic dispenser.
Contact us about the most suitable method for dispensing paste onto a particular component; we can then formulate the paste accordingly.
The size and shape of paste deposits
The shape and design of the component govern the size and placement of the paste deposit. It is often possible to calculate an approximate amount of paste required per joint. However, in most cases a simple production test will quickly establish the correct amount to use.
Automatic dispensing
If possible, paste should be applied as a single deposit. This method needs the minimum of dispensing equipment and the least time spent on the dispensing operation.
On long joints, it may be necessary to apply more than one paste deposit. This increases the area covered by flux and alloy and is advisable particularly if the alloy is not free flowing.
Paste can be applied as a number of dots, or as a continuous stripe. In applications such as this, movement of either the dispensing nozzle or the component itself may be required during paste application.
Heating methods for brazing and soldering paste
Our paste products can be used successfully with most of the standard heating methods.
- Fixed burners – accurate and reproducible heat patterns can be set electronically using a range of fuels. They may be arranged as single or double burners on basic shuttle or rotary indexing machines.
- Furnace heating - uses a reducing atmosphere or vacuum to prevent or break up surface oxides during the brazing process.
- Induction heating - quick and easily controlled heating well suited to paste products.
- Resistance heating – works well with brazing and soldering pastes. Resistance heating with a separate filler metal and flux can cause problems because the flux acts as an insulator. Using paste will help to overcome this as the finely divided powder offers a conductive path through the flux.
- Hand torch - pastes should be heated indirectly to ensure the paste deposit reaches the correct temperature at the same rate as the rest of the component. If heated directly, the flux in the paste will not have sufficient time to clean the parent metals and the molten filler metal alloy will not wet out onto the joint area.
Heating brazing paste
The behaviour and flow characteristics of a brazing paste when heated will depend upon its formulation, whether it contains flux and the heating method being used. A typical fluxed paste for brazing in air with a silver brazing filler metal based around the 'B1' binder system will go through the following stages:
- On initial heating, the paste deposit will increase in size. During this early stage of heating the paste deposit should be heated slowly and indirectly to cause it to 'set'. Heating it too rapidly or directly can cause it to 'explode' or spit.
- With further heating, the paste will either start to smoke, or if a flame is present ignite. Where ignition of the paste does not occur, for example when using RF induction or resistance heating, local exhaust ventilation should be used to remove the fume from the working environment.
- As the heating continues the paste's appearance will change from a shiny, glossy deposit, to a dull, dry one. The binder has now been lost from the paste which has become 'set'. Once 'set' it is stable and can be subjected to a more rapid rate of heating.
- Next the flux starts to melt, 'wetting' the parent metals and reducing surface oxides on them. Initially this takes place locally around the base of the paste deposit. As the temperature continues to increase the flux becomes more fluid, spreading out and flowing into the capillary gap present within the joint.
- Finally, as more heat is applied the filler metal will begin to melt and then flow completely. The rate of heating at this stage needs to be sufficient to prevent liquidation of the filler metal. This is where the filler metal only partially melts leaving behind a skull of solid material and resulting in a joint that is only partially filled.
Both the binder and the flux in a paste can be changed or modified to match the needs of a particular brazing job. For example, binder systems can be supplied that collapse and spread onto a component where paste is needed over a large area.
Removal of brazing paste residues after heating
The flux residues of brazing pastes are corrosive and therefore their removal after brazing is essential. They are similar to those generated in other brazing operations and may be removed by the same methods - soaking in hot water (> 40oC for 30 minutes), soaking in 10% sulphuric acid or by mechanical removal (e.g. grit blasting). The method should depend on the type of flux present. Brazing pastes often leave a 'footprint' or mark on the component that is difficult to remove after brazing. For advice on the best method of removing the flux residues please contact us.
Heating soldering paste
Solder pastes are formulated around totally different binder systems and flux types to those used for brazing and they therefore react completely differently when heated.
Solder paste when heated initially will exhibit some slump depending upon its formulation. With further heating the deposit may bubble and heave (foam) and begin to smoke. Local exhaust ventilation should be used to remove the fumes. If heated too rapidly the paste deposit can boil and spit. Gentle, indirect heating (such as hot air heating) is recommended throughout the soldering process.
The solder paste becomes more fluid as the temperature is increased but it should remain colourless throughout the soldering operation. If the flux starts to go brown it is an indication that either it is beginning to become exhausted or that the paste has been overheated.
As the solder alloy within the paste begins to melt, the flux is displaced from the joint and floats on top of the molten solder. Fluxes and solders will always flow to the hottest point of a joint and further flow of the solder into, along or around the joint can be encouraged by creating a thermal gradient across it.
If the solder fails to wet and flow as required or forms a molten 'ball' then this is an indication that the flux has not been able to remove the oxides present on the surface of the parent materials.
This could be due to exposing the paste deposit to too high a temperature or exhausting the flux before the filler metal becomes molten. Alternatively, an inappropriate fluxed binder system was selected for the application.
Removal of soldering paste residues after heating
Flux residues from soldering paste are classified as non-corrosive, intermediate or corrosive. Non-corrosive residues may be left on the completed joint. Intermediate or corrosive flux residues should be fully removed. Warm water, mildly alkaline solution, or in the case of rosin based flux residues an organic solvent, should be used. For advice on the best method of removing the flux residues please contact us.
Storing and shelf life
Brazing and soft soldering pastes have limited shelf life and strict stock rotation should be exercised during their storage. The binder system and the filler metal powder can separate and the paste may dry out during storage. Separation or drying out of a paste is more likely if the product is not stored correctly.
Storage temperature
Braze and soft solder pastes should not be stored below 5°C or above 25°C. The ideal storage temperature for pastes is between 10 and 15°C. The viscosity of brazing and soft solder pastes is affected by temperature. They are designed for use between 18 and 24°C (Viscosity measurements are taken during production at 20°C). If subjected to temperatures below 15°C the paste viscosity will increase making dispensing more difficult. If stored at temperatures above 25°C the paste will become very fluid and may separate and dry out. It is therefore recommended that pastes should be withdrawn from the storage facility some time before use and placed in the workshop environment to obtain a normal working temperature. Storing at temperatures below 5°C can result in damaging the products irreparably.
Storage conditions
- Paste should ideally be stored in cool dry conditions away from direct sunlight and other sources of heat.
- Pastes supplied in buckets or pots should be stored in closed containers and stood with the lid upper most.
- Pastes supplied in machine cartridges or hand syringes should be stored standing up in racks with the 'follower plug' upper most and the nozzle facing down. Storing cartridges / syringes on their side can result in separation of the paste.
FAQs
Can brazing filler metals give colour matching for different metals?
For some applications a colour match between the brazing filler metals and the parent metals is clearly desirable. The following SILVER-FLO alloys should be considered.
- SILVER-FLO 60, 56 and 55 are silvery in colour and are suitable for use on nickel silver or stainless steel provided that there is no danger of interfacial corrosion
- SILVER-FLO 20, 18 and 16 are more yellow or brass coloured. Consequently they are a reasonably good colour match for brass but the melting point of the brazing filler metal can be relatively close to that of the parent metal.
Can other filler metals be used to avoid interfacial corrosion?
There are several other types of filler metals that can be used to avoid the potential problem of interfacial corrosion:
- OROBRAZETM products
- PALLABRAZETM products
- B-BRONZETM and C-BRONZETM filler metals
- Soft Solders like P40TM
- Gold based brazing filler metals
- Palladium based brazing filler metals
- Copper based brazing filler metals
- Silver/tin filler metals
Can you recommend filler metals for sequential or step brazing?
To build up an assembly in two or more brazing operations, it may be necessary to use brazing filler metals with successively lower melting points. This technique will avoid disturbing the previously brazed joints. There are a number of filler metals which have short melting ranges and are ideal for this work:
- First brazing operation: SILVER-FLO 18 (784-816˚C)
- Second brazing operation: SILVER-FLO 33 (700-740˚C)
- Third brazing operation: SILVER-FLO 55 (630-660˚C)
SILVER-FLO 24, 20 and 16 are also suited to step brazing.
How can I improve the wetting of brazing filler metals onto cemented tungsten carbide?
The cemented carbide will be more easily wetted by the molten brazing filler metal if the surface is ground shortly before brazing then degreased and kept clean before applying flux.
The degree of wetting of brazing filler metal onto a cemented tungsten carbide piece will depend on its composition. Cemented tungsten carbides with small additions of titanium or tantalum carbide are more difficult to wet than standard carbides.
Wetting can be improved by the use of brazing filler metals containing nickel or manganese (e.g. ARGO-BRAZE 49H) and special boron modified fluxes such as TENACITYTM No.6 Flux Powder or Paste. Plating or coating the carbide with an easy to wet metal such as copper or nickel can also help overcome this problem.
In general when brazing cemented tungsten carbide a heating pattern should be employed which brings both components to brazing temperature at the same time. Care should be taken to avoid overheating the cemented tungsten carbide component as this will increase stresses. Once the brazing filler metal is molten it is advisable to move the carbide slightly to improve wetting and displace trapped gas or flux.
What brazing filler metals are recommended to avoid interfacial corrosion?
In general terms, when brazing stainless steels in air with a flux, normal silver filler metals from the SILVER-FLOTM and EASY-FLOTM ranges are the least resistant to interfacial corrosion. Silver brazing filler metals containing nickel have been found to offer greater resistance particularly on austenitic steels. ARGO-BRAZETM 56 and ARGO-BRAZE 63 are particularly recommended to help avoid interfacial corrosion.
What considerations are there for brazing filler metals that contain tin or silicon?
Tin containing filler metals are 'hot-short' and may be prone to cracking if quenched from high temperatures (in excess of 300˚C). This is particularly the case with filler metals with medium or high brazing temperatures. They should not be quenched when used to braze components with widely differing coefficients of thermal expansion.
Filler metals containing silicon may be used to braze steel assemblies but are not recommended where steel components are subject to high impact or fatigue stress in service as the silicon forms a brittle iron intermetallic.
What filler metals are suitable for sea water or marine environments?
When brazing assemblies come into contact with sea water and other aqueous solutions with a high ion concentration, it is important that both the parent metal and the brazing filler metal are resistant to dezincification.
Johnson Matthey undertook research work during the 1940's and discovered that the filler metals SILVER-FLO 60, 56, 55, 452, 44 and 43 all offer excellent resistance to dezincification. Consequently these filler metal alloys have found uses in brazing of marine pipes and fittings in offshore installations and in shipbuilding.
Of these filler metals SILVER-FLO 55 is the most widely used because it has a low brazing temperature and excellent flow characteristics.
What is interfacial corrosion and what types of steel are affected?
Interfacial crevice corrosion is a particular type of failure where silver brazed joints in stainless steel are exposed to water or humidity in service. In these conditions joint failure may result along the stainless steel - brazing filler metal interface.
To produce a joint failure by interfacial corrosion three criteria need to be satisfied:
- At least one member of the joint must be made from a stainless steel.
- The brazing filler metal must be susceptible to this form of attack.
- The completed joint must be exposed to damp or wet environments in service.
All types of stainless steel are susceptible to attack by interfacial corrosion. The nickel free, or low nickel ferritic and martensitic type stainless steels (e.g. types 403, 410, 416, 420, 430, 431) are most susceptible to interfacial crevice corrosion.
Austenitic grades of stainless steel (e.g. types 302, 303, 304, 316, 321) are more resistant. Failures with these grades are rare provided the correct brazing alloys are chosen.
What is stress cracking or intergranular penetration in a brazing context and how is it avoided?
Nickel and nickel-based alloys are susceptible to cracking during brazing with silver brazing filler metals. This cracking is often known as inter-granular penetration or stress cracking. High nickel content copper alloys, such as 70:30 cupro-nickel, are also prone to this type of failure. Removing the source of stress will eliminate the problem.
SILVER-FLO 60 is recommended where freedom from stress cannot be guaranteed. The relatively low zinc content and high brazing temperature make it less likely to initiate stress cracking.
What steps can be taken to avoid cracking in cemented tungsten carbide?
Here are three steps that can be taken to avoid cracking in tungsten carbide segments:
1. Joint design to help avoid cracking
Increasing the joint clearance will provide a thicker layer of ductile brazing filler metal capable of accommodating the stresses from differential expansion.
On large carbides the use of thin backing materials can lead to cracking because they are not able to withstand the high stress resulting from contraction on cooling. Thicker backing materials or bodies to hold the carbide can reduce the incidence of failure. With long lengths of carbides bending or cracking can be a problem. Consideration should be given to the use of multiple pieces of carbide to overcome this.
2. Filler metal selection to help avoid cracking
Conventional free-flowing brazing filler metal alloys such as Silver-floTM 55 capable of filling joint gaps of 0.05mm are satisfactory for brazing carbide with a length of up to 9mm.
Larger sized carbide pieces can be stressed to such an extent that cracking occurs during brazing or in a subsequent grinding operation. For these applications the joint must be artificially thickened. Using either a less free-flowing brazing filler metals such as Argo-brazeTM 49H or a tri-foil brazing material can do this.
3. Cooling and finishing
Slow uniform cooling of the carbide is always recommended to avoid stressing and possible cracking. Quenching in water is not recommended. It is advisable to avoid thermal stresses during grinding and finishing of the carbide component.
Why does cracking occur in tungsten carbide after brazing?
Tungsten carbides have low coefficients of thermal expansion compared with that of steel. This means that they expand and contract less than steel does during heating and cooling. As a result stresses can be built up in the carbide. The magnitude of the stresses created by the differences in expansion will be a function of the size of the piece of carbide being brazed. This can give rise to cracking of the carbide during or following brazing operations.
Get in touch
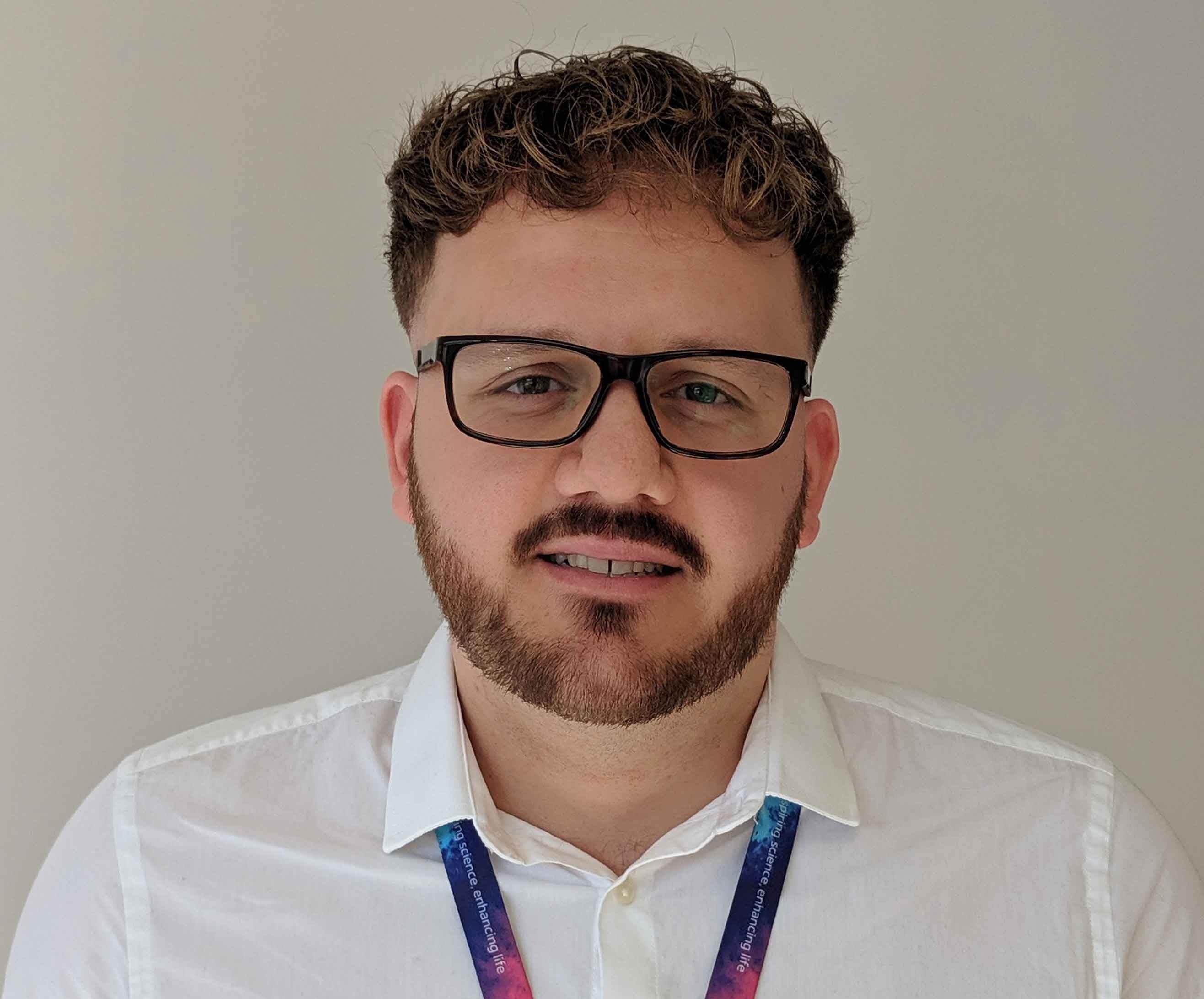
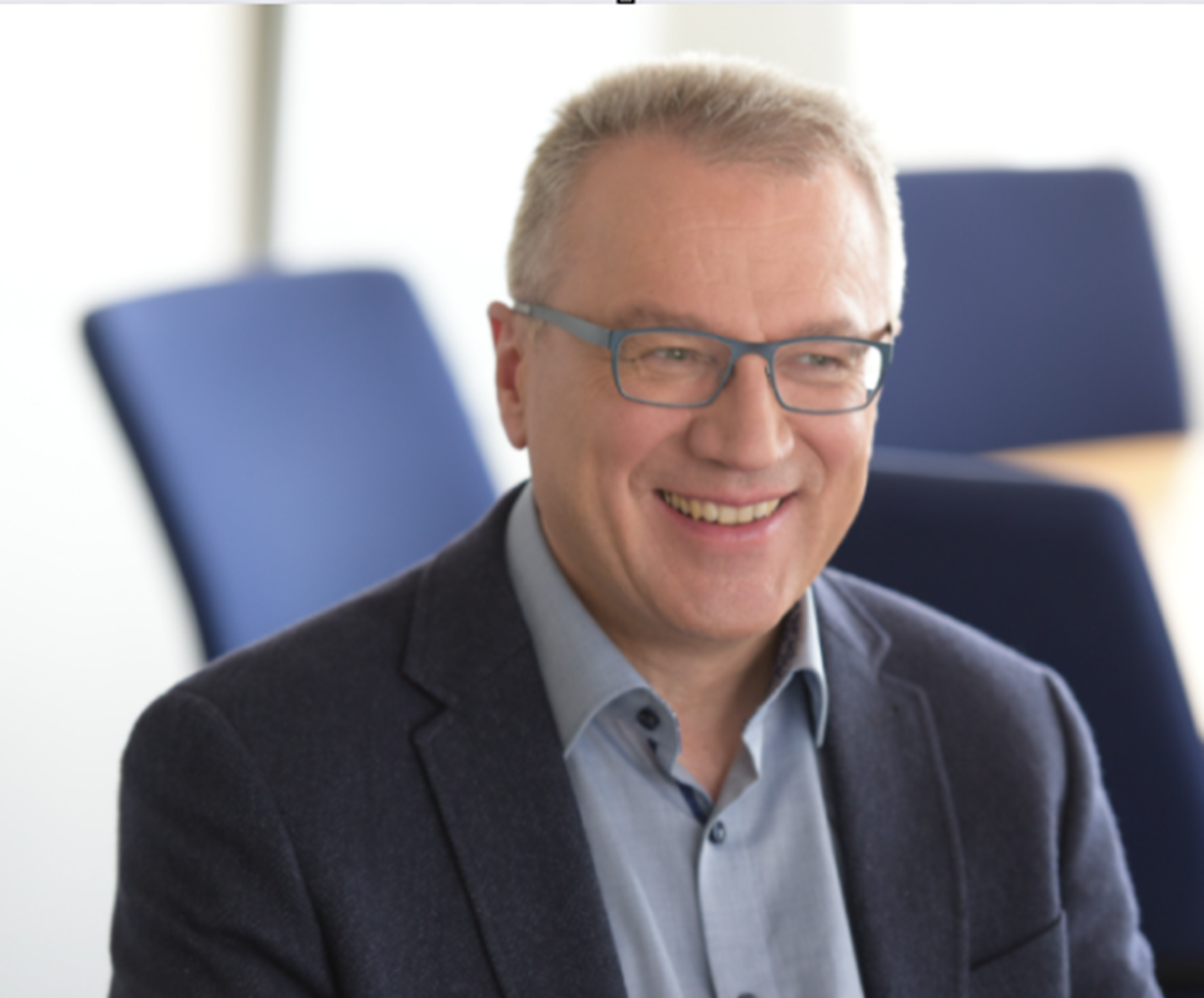