Striking a balance in clean hydrogen production
Peter Ellis, Technology Director for Green Hydrogen, discusses the decarbonisation of the hydrogen industry and the technological trade-offs and decisions that must be considered to achieve this goal.
20 December 2021
The challenge presented to achieve net-zero emissions is real and countries around the world must do absolutely everything in their collective power to hit this target. Policy makers globally have begun communicating their strategies and roadmaps for achieving net zero by 2050, with low carbon hydrogen having a major part to play. Why is this? It is a recognition of the role sustainable hydrogen can have in decarbonising end uses where, for example, direct electrification is not successful, where hydrogen is used as a chemical, where energy needs to be stored for more than a few hours, or moved from where it is generated to where it is used.
A growing market
Demand for hydrogen has grown more than threefold since the 1970s and continues to rise. The International Energy Agency reports that demand for hydrogen in its pure form is approximately 70 million tonnes per year. Currently this hydrogen is almost entirely supplied from fossil fuels, with 6% of global natural gas and 2% of global coal going to hydrogen production. Consequently, the production of hydrogen is responsible for approximately 830 million tonnes per year of carbon dioxide (CO2) emissions, over twice the CO2 emissions of the United Kingdom. In energy terms, total annual hydrogen demand worldwide is around 330 million tonnes of oil equivalent, larger than the primary energy supply of Germany.
Changing the way in which hydrogen is produced can prevent a huge portion of today’s CO2 emissions and enable the hydrogen market to grow without exerting an additional burden on the environment for future generations. This can be achieved by building new or retrofitting existing fossil fuel-powered hydrogen plants with carbon capture and storage systems (CCS), more commonly referred to as blue hydrogen, or extracting hydrogen from water molecules through electrolysis powered by renewables, known as renewable hydrogen or green hydrogen.
The growth and optimisation of these low carbon hydrogen technologies will enable the decarbonisation of the existing hydrogen market and other hard-to-abate sectors where electrification is not an attractive option, whilst also ensuring that new applications for low carbon hydrogen can evolve. New applications could include hydrogen as a transport fuel, replacing natural gas for heating and using hydrogen as an energy vector to store and move renewable energy. There are so many diverse opportunities for low-carbon hydrogen that it is difficult to predict how far it can ultimately go.
Options for electrolysis green hydrogen production
Green hydrogen is produced using energy from renewables, such as wind and solar, to split water into hydrogen and oxygen gases in a device known as an electrolyser. There are several different electrolyser technologies available but the two most frequently used now are alkaline water electrolysis (AWE) and proton exchange membrane (PEM) electrolysis.
PEM electrolysers use platinum group metal (pgm) catalysts applied in ultra-thin layers to a polymer membrane to achieve the key reactions producing high-purity hydrogen. They have a smaller relative footprint than alternatives and are flexible in operation, hence their ability to harness the intermittency of renewable energy effectively.
Alkaline electrolysers use an aqueous electrolyte solution such as potassium hydroxide or sodium hydroxide in a cell to produce hydrogen. This is a mature and well-understood technology with a lower capital cost today, but typically produces lower purity hydrogen than PEM, generally with a larger footprint and less flexible operation.
Other slightly less mature technologies include anion exchange membrane (AEM) electrolysis, which has the potential to offer many of the same benefits as PEM electrolysis without using pgms as catalysts or in other parts of the system, and solid oxide electrolysis (SOEC) technology which uses solid ceramic material as the electrolyte operating at temperatures in excess of 600°C, making it well suited to applications where heat is available, such as in combination with nuclear power.
Considerations for system optimisation
At the heart of every PEM electrolyser is a catalyst coated membrane (CCM) which is responsible for the conversion of water into hydrogen and oxygen. CCMs consist of a polymer membrane and precisely engineered layers of structured platinum and iridium oxide catalysts. The catalysts are applied to the membrane which uses electrical energy in the most efficient way.
The key to achieving an optimal system is not just combining the most advanced individual components but optimising each component and the way the CCM is assembled based on the end use operating requirements, balancing the trade-offs and design choices that exist for electrolyser owners and operators.
End use
What is meant by end-use operating requirements? Consider two very different uses of hydrogen. Firstly, a hydrogen refuelling station with an electrolyser in situ will need very high purity hydrogen so as not to damage the fuel cells, and the system may not need to run 100% of the time if storage is available, but ultimately it will need to be flexible and produce low-cost hydrogen for consumers. Compare this to a large ammonia production facility where the electrolyser may need to run 100% of the time to keep up with in-production demand and prevent outages. In this case the primary requirements could be a robust and durable system to prevent unscheduled and expensive maintenance stoppages.
When considering CCM design, these operating requirements must be balanced with multiple trade-offs and design choices including: efficiency, durability, and both capital cost (CAPEX) and operating cost (OPEX).
Efficiency in this case means how much power is needed to make a unit of hydrogen and directly influences the cost of the hydrogen that is produced. The efficiency of the electrolyser system is impacted by various properties of the CCM, including membrane thickness, membrane additives, and catalyst effectiveness. Johnson Matthey can tailor membranes to it’s customers’ needs, offering reinforcements, recombination catalyst layers, radical scavengers, and a range of thicknesses to suit multiple applications.
The durability of the CCM can be improved through increasing the thickness of the membrane or increasing the catalyst loading. However, both of these activities will increase the CAPEX of the system. JM uses membrane additives to increase the durability of its CCMs, and the company is developing next-generation catalysts which will be more stable under operating conditions, helping lower overall system costs.
Electrolyser design
Another area sometimes overlooked, and one that adds to the CAPEX, is electrolyser design. It is important that electrolyser engineering designs take into account CCM production methods, facilitate efficient manufacture, easy reproducibility and low in-production waste. For example, producing a circular electrolyser offers benefits in high pressure operation from an engineering perspective but this can create significant CCM production waste (more so than square or rectangular designs), which increases the overall cost of the CCMs.
It is therefore key for electrolyser producers to work with the supply chain, including the CCM supplier, to ensure that the right balance of performance is achieved in the chosen application. JM works with electrolyser producers and, in some cases, their customers to ensure that this balance is achieved.
Once the balance of trade-offs has been set, it is also very important that circular economy principles are incorporated into the system design, working together across the supply chain to enable recycling and the ability to reuse as much of the electrolyser as possible. In this way, the carbon footprint created by the manufacture of electrolysers themselves can be minimised.
Conclusion
There are still many challenges to overcome. To be successful means addressing the trade-offs that exist today and facilitating the growth of tomorrow. On the hydrogen production side, the levelised cost of low-carbon hydrogen must be reduced significantly (ideally to approximately $1/kg or lower), using new technology approaches for CCMs and their components, and next-generation manufacturing techniques which unlock new products and use raw materials ever more efficiently. Electrolyser system developers and end users must be supported in achieving their goals, whether they are for grid balancing, chemicals production or heating and fuelling applications.
The time for action is now, working together to achieve the energy transition goals globally. Balancing customer needs and the trade-offs faced in green hydrogen production must be discussed openly to ensure that scale-up and cost-down can happen quickly.
Johnson Matthey has a vision, for a world that is cleaner and healthier, for today and future generations. The science and engineering the company deploys cuts across numerous parts of the hydrogen value chain, including hydrogen production catalysts, components for hydrogen fuel cells and electrolysers, and new technologies for low carbon hydrogen production, including both blue and green routes.
This article was originally published in the Winter 2021 issue of Energy Global, December 2021
Read more
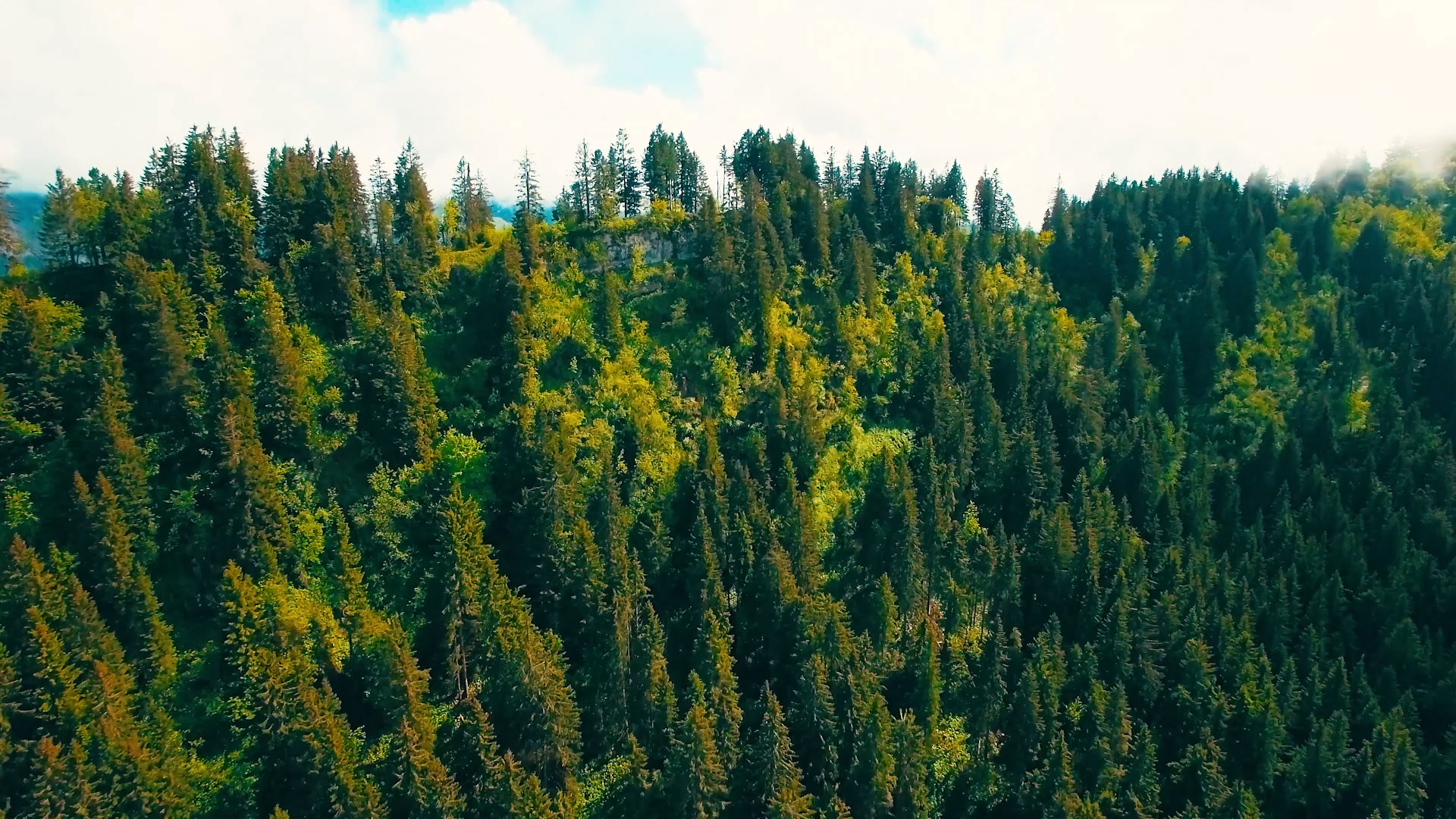