What are Johnson Matthey’s activities across the hydrogen value chain?
Johnson Matthey has been involved in the hydrogen space for decades and our experience cuts across many parts of the value chain. In hydrogen production, we have a market leading position in catalysts, and we have new technologies for blue and green hydrogen production. Once produced, transporting and distributing this key molecule is challenging; our process technologies are helping navigate this by transforming hydrogen into energy carriers. And in hydrogen applications, we develop and manufacture the key components at the heart of hydrogen fuel cells and our catalyst and process technology is used to transform hydrogen into chemicals and fuels.
Blue hydrogen
In blue hydrogen, our LCHTM technology has best-in-class environmental and economic credentials. It enables low carbon hydrogen production with up to 98% of the produced CO2 captured as a high pressure, high purity stream. The CO2 can then be stored in oil fields, or it can also be an excellent source as a raw material for transforming into chemicals and fuels.
Our LCH technology offers striking advantages including:
- High efficiency, resulting in lowest natural gas usage per unit of hydrogen
- Optimised design reducing CAPEX by 40% compared to conventional steam methane reforming technologies coupled with carbon capture
- A very low carbon footprint. In fact, recent analysis by the Hydrogen Council shows that autothermal reforming-based options, like JM’s LCH technology, can compete with solar green hydrogen in a life cycle analysis.
And crucially this technology is deployable today, allowing us to start moving to net-zero. For example, our technology is being used in the HyNet project – the UK’s first low carbon hydrogen plant – which is set to have an 80 kt per annum capacity.
Fuel cell technology
Our fuel cell technology dates back to almost when Johnson Matthey was first founded. We supplied the platinum when William Grove first demonstrated a fuel cell in the 1830s. And in the 1960s, Johnson Matthey even supplied the electrocatalysts for the fuel cells that provided onboard power for the Gemini and Apollo Space Missions.
Over the last two decades, we’ve been developing fuel cell technologies globally, supplying the catalyst coated membranes (CCMs) and membrane electrode assemblies (MEAs) that are the performance-defining components at the heart of a proton exchange membrane (PEM) hydrogen fuel cell.
We’re the only MEA supplier in the industry with in-house catalyst and membrane technologies. This enables us to customise our offering to meet our customer’s specific requirements. Success in the fuel cells market rests on building collaborative relationships with our customers, working closely to solve the challenge of balancing often competing demands of performance, durability and cost. Since 2005, Johnson Matthey has participated in over 50 fuel cell development programmes, collaborating with the world’s leading automotive brands to advance fuel cell technology and manufacturing processes.
Green hydrogen electrolyser technology
Green hydrogen is produced using energy from renewables, such as wind and solar, to split water into hydrogen and oxygen gases in a device known as an electrolyser.
We launched our green hydrogen business in 2020; entering the PEM electrolyser space was a natural step for us. Building on our experience in fuel cells and platinum group metal chemistry, we design and manufacture innovative CCMs for green hydrogen production, at scale, incorporating our proprietary membrane technology and market leading catalysts.
How do your underlying capabilities in platinum group metal (PGM) chemistry support the hydrogen economy?
Johnson Matthey is a specialist in PGM chemicals and electrochemistry for hydrogen technologies. Using our extensive understanding of surface chemistry, material design and catalysis, we make platinum and iridium catalysts – the foundation of the CCMs/MEAs that generate green hydrogen and use hydrogen as a clean fuel. We’ve developed these to give exceptional performance for the lifetime of the cell. We also make platinum salts that protect the electrolyser from degrading, extending its lifetime.
As experts in PGM refining and recycling, with over 200 years of materials science and metallurgy experience, we can efficiently recover and refine PGMs at the end of the economic lifetime of the relevant components. Our circular solution ensures these precious metals can be reused again and again.
Our core capabilities are strongly reflected in our research and development function, where we have about 1,500 dedicated colleagues supporting innovation and development of technologies for all our businesses. In the area of PGM chemistry, we’re focused on metal thrifting, meaning using as little precious metal as possible whilst still achieving the same performance. This will help reduce the overall cost of the fuel cell or electrolyser stack and increase the adoption of these technologies.
How does your PGM recycling business help support your customers?
For fuel cells and electrolyser components, security of supply of platinum group metals is key, especially platinum and iridium. As the world’s largest recycler of PGMs, we are working on recovering precious metals from the entire lifecycle of fuel cells and electrolysers, from production to end-of-life, then refining the PGMs so they can be reused in our catalysts. There is zero difference in performance between recycled and fresh materials, giving place to an endless loop for PGM availability. This will become increasingly important as the market for hydrogen technologies scales up and demand for these raw materials rises.
Of course, one of the benefits of using recycled metals is the lower carbon footprint. The carbon intensity of recycled metals is only about 2% of primary metals (Source: IPA), so we’re also offering our customers low carbon manufacturing routes that will help them meet their sustainability targets.
We also have exceptional expertise in both market insight and precious metal management services, helping to secure access to these critical raw materials as demand grows - enabling the hydrogen economy.
What is JM’s most exciting recent achievement/partnership in the fuel cell space?
The fuel cells market for commercial vehicles is growing very rapidly. Over the last few years the fastest growth has taken place in China. According to a report published last year by the International Energy Association of all the fuel cell buses on the roads globally by year end 2020, 93% were operating in China. In the medium duty commercial vehicle segment over 99% of fuel cell trucks were operating on China’s roads. In the heavy duty segment just 14 trucks were in operation globally, all of them in Europe. All of these trucks were demonstration projects.
However, an example of how quickly the market for heavy duty fuel cell vehicles is developing is our partnership with REFIRE – a leading supplier of hydrogen fuel cell technologies. Between April and September 2021, 170 new heavy duty fuel cell electric vehicles (FCEVs) hit China’s roads powered by REFIRE and Johnson Matthey technology. And this number is expected to increase over the coming months.
Why do you think China’s fuel cell heavy duty vehicle market is developing faster than the European one?
One factor is the limited domestic sources of oil and gas in China. As China becomes more energy independent, they are looking for alternative power sources. China has already made strides in renewable energy and has ambitions for making green hydrogen at large scale.
China is aiming to reach net zero by 2060. To achieve this goal the government is providing significant support to build the market for hydrogen production, distribution and the manufacturing of FCEVs. For example, the Chinese government recently announced a new subsidy program around some major municipality clusters to encourage the development of hydrogen refuelling stations and the manufacturing of FCEVs locally.
In November last year, Johnson Matthey started collaborating with UNIDO’s International Hydrogen Energy Centre who are working towards building the hydrogen economy in China and other developing nations.
What can you share about the lifetime of your fuel cell components?
The nascent market for FCEVs means that there is limited on-the-road data against which to benchmark performance. There are now over 1,300 FCEVs on the road in China containing components supplied by Johnson Matthey and it is estimated that these vehicles have travelled over 6.5 million kilometers.
Johnson Matthey pays special attention to its catalyst and membrane development processes to maximise lifetime. We work with our customers to make sure that the CCM and the assembly are sufficiently robust, aiming to secure the best performance and durability.
Development in this space is remarkably fast at both the catalyst and the assembly level. We’re working in collaboration with our partners as part of the IMMORTAL project to develop high performance fuel cell components for heavy duty vehicles with 30 thousand hours of operation lifetime or about the 1-million-mile mark.
How have your hydrogen production businesses evolved over the last five years?
Our journey in CCS-enabled (blue) hydrogen started several years ago when we developed our award-winning LCHTM technology. This is based on the smart combination of existing unit operations from our syngas technology portfolio. Our technology has been designed specifically for low carbon hydrogen production and is deployable today. Recently we have seen substantial interest in our offer from customers across the globe.
Over the past two years, we’ve been building our electrrolysis (green) hydrogen business. We’ve expanded our manufacturing capacity through the acquisition of the Oxis Energy site in Oxford and have announced many partnerships with leading stack and electrolyser manufacturers as we build up our technology offering and grow the business.
Can you share an example of a recent achievement or partnership in hydrogen production?
Our LCH™ technology is being used in the HyNet project. This project was recently selected by the UK Government as a Track-1 cluster, meaning it will start decarbonizing industry by 2025. The UK is one of the leaders in low carbon hydrogen, with a mix of natural gas, depleted oil wells to store CO2 and government support. I expect the UK projects to be some of the first in the world demonstrating a hydrogen economy. We are seeing more geographies driving their hydrogen plans, with global interest in our technology including North America, Russia and North East Asia.
In electrolysis (green) hydrogen, we’ve announced many great partnerships with leading players to develop advanced electrolyser components including Plug Power, Hoeller Electrolyzer and HyStar. And I’m really excited to see what we can achieve together.
How do you see the future of hydrogen production?
There is a huge focus on climate change at the moment. Every CO2 molecule that we can prevent from escaping into our atmosphere, is a molecule that won’t contribute to climate change. We recognise that hydrogen has a key role to play in the transition to a cleaner world and that’s why recently Johnson Matthey pledged to invest 1 billion in clean hydrogen technologies by 2030.
It won’t be a one size fits all approach. Regional differences mean the production of low carbon energy will vary across the globe. Countries with access to natural gas or oil fields for CO2 storage are well suited to CCS-enabled (blue) hydrogen. And countries with good access to renewable energy will be looking at electrolysis (green) hydrogen.
Importantly, while we work on developing electrolysis (green) hydrogen to be able to roll it out at a significant scale, CCS-enabled (blue) hydrogen technologies with a low carbon footprint – like Johnson Matthey’s LCHTM technology with up to 98% lower CO2 emissions compared to conventional (grey) hydrogen production – are available now to enable clean hydrogen production.
What’s the main challenge to face in the short and medium term for Johnson Matthey in hydrogen?
The challenge is how to make sure that society can effectively develop the infrastructure behind a hydrogen economy. We need to see the cost of renewable electricity reduce to enable green hydrogen production at scale, and we need to build hydrogen transportation systems and refuelling infrastructure for mass deployment of hydrogen-powered vehicles.
Right now, several projects in the UK, including HyNet, are working to demonstrate a hydrogen economy on a regional scale, including hydrogen production, transport, storage and fuelling. We need projects like these to make sure deployment can take place simply and quickly.
Global alignment of hydrogen infrastructure, for example industry norms and standards for transportation and storage, will be crucial to accelerate development of the hydrogen economy. Worldwide standardisation will give clarity to businesses, maximise the connection of production and end-use, and reduce cost.
Any Closing thoughts to share with our Hydrogen Central readers?
In addition to our technologies for hydrogen production and fuel cells, at Johnson Matthey we see hydrogen as an enabler for the decarbonisation of the chemicals and fuels industries.
If renewable electricity is available and you have water, you can produce hydrogen. And if CO2 is produced on-site in areas that are hard to decarbonise, or from sustainable sources like municipal solid waste, or even from direct air capture, you can transform that carbon dioxide into carbon monoxide. Then the result would be CO and H2, otherwise known as syngas. Syngas is the building block to create commodity chemicals needed for everyday life, like methanol and formaldehyde. And JM’s catalyst and process technologies for making these chemicals are suited to sustainably sourced syngas. So, building the hydrogen economy is also about offering a sustainable solution to the chemicals and fuels industries.
Interview originally published by Hydrogen Central - 3rd February 2022
Read more
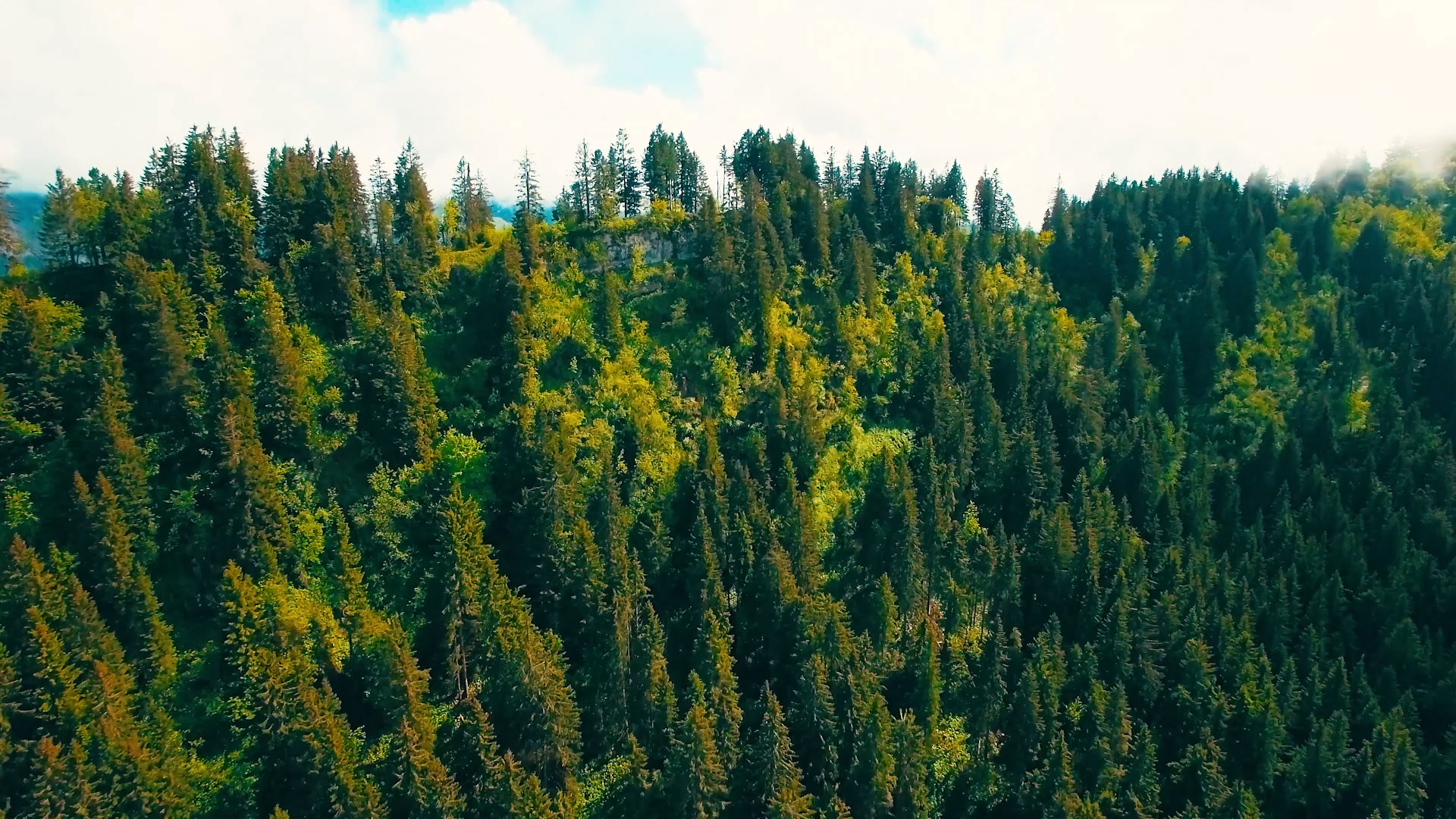