Diesel particulate filter
A diesel particulate filter (DPF) removes particulate matter from diesel exhaust by physical filtration. Many filter types are available but the most common type is a ceramic (cordierite or silicon carbide) honeycomb monolith.
The structure is like an emissions catalyst substrate but with the channels blocked at alternate ends. The exhaust gases must therefore flow through the walls between the channels and the particulate matter (PM) is deposited on the walls.
The filtration efficiencies of diesel particulate filters is >99% for solid matter. Since diesel particulate matter has a non-solid portion, the total efficiency for this is lower than this >90%.
All particulate filter systems include some means of regeneration.
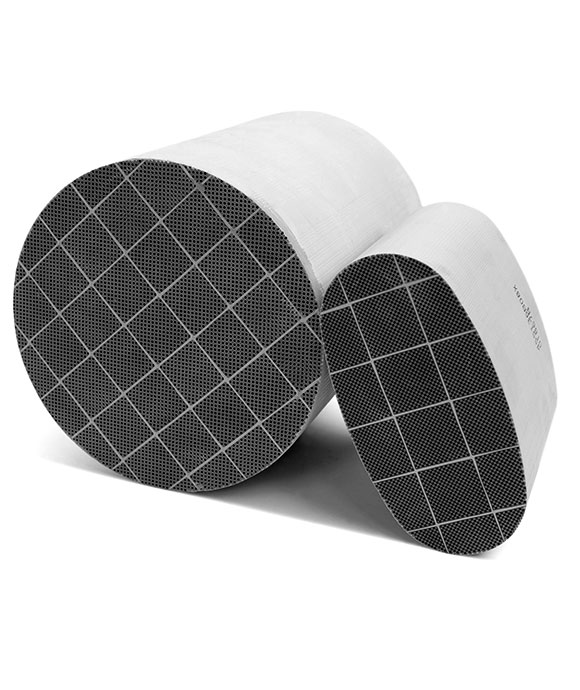
Filter regeneration
Any filter has a finite capacity. Diesel particulate filters (DPF) must be cleaned out, intermittently or continuously, if they are not to block. This is most important, since an overfilled filter can damage the engine through excessive exhaust back pressure and can itself be damaged or destroyed.
The material trapped in the filter is in most part carbon particles with some absorbed hydrocarbon.
There are two principle techniques for removing the particles:
Combustion with oxygen (O2)
- [C] + O2 → CO2
Combustion with nitrogen dioxide (NO2)
- [C] + NO2 → CO2 + NO
NO2-based systems are greatly favoured because the reaction takes place at temperatures seen in most diesel exhausts.
The leading DPF system around the world is Johnson Matthey's Continuously Regenerating Trap® technology (CRT®) which uses an oxidation catalyst in front of the filter to generate the NO2 required to keep it clean.
Passive and active regeneration
DPF systems that are able to regenerate themselves using only the exhaust gas stream and without additional energy inputs, are known as passive systems.
The CRT system is able to function in a wider range of conditions than any other passive system and this is the basis of its success. Its advantage is most clearly seen in applications with low exhaust temperatures.
Passive systems are favoured, particularly for retrofit applications, because they require no integration with the engine, no source of energy other than the exhaust gases themselves, and no complicated control systems.
Applications with variable or unreliable duty cycles, or with exhaust conditions not suitable for passive systems, require active regeneration.
Passive systems
Continuously Regenerating Trap system
The Continuously Regenerating Trap (CRT®) system is the most widely used diesel particulate filter (DPF) system in the world and is a patented Johnson Matthey technology.
It comprises an oxidation catalyst followed by a diesel particulate filter (DPF).
The oxidation catalyst removes CO and HC and oxidises some of the NO in the exhaust gasses to NO2. This NO2 then reacts with the particulate matter (PM) trapped in the filter, producing NO and CO2 and cleaning the filter.
Johnson Matthey has many years of experience of specifying CRT systems for diverse applications and is able to advise on which system is most suited to individual applications.
Active systems
Active DPF Regeneration
Any application, in which it cannot be guaranteed that the exhaust gas conditions will be suitable for a passively regenerating system, will require some active regeneration. Even in these cases, it is desirable to maximise the amount of passive regeneration that can be achieved since passive regeneration is 'free', requiring no additional energy.
Almost all active filter regeneration techniques operate by raising the temperature of the filter to around 600°C. This is the temperature at which the particulate matter (PM) collected in the filter, will combust in oxygen.
Combustion of HC over a catalyst
The CRT and CCRT® systems can form part of actively regenerated DPF systems in which the HC content of the exhaust stream is periodically enriched, either by in-cylinder post injection or by direct injection of fuel into the exhaust stream. The HC is burnt over the catalyst, raising the temperature of the DPF to combust the collected PM.
Johnson Matthey has developed a range of catalysts specifically for this type of system.
These systems require careful control of the HC enrichment of the exhaust stream and are therefore much more suitable for OE applications than for retrofit systems.