Diesel engines are a valuable power source but their emissions can be a disadvantage. These emissions are best dealt with at source through the use of exhaust after-treatment.
Johnson Matthey works with engine and equipment manufacturers to provide emissions control systems for a variety of non-road NRMM applications.
Our engineering experience and catalyst expertise enable us to provide solutions for a wide range of requirements, from a few systems for specialist applications to standard fit components for regulatory emissions compliance.
Johnson Matthey’s range of systems for construction equipment and other non-road machines ensures that there is a system suitable for every application.
These applications include:
Construction | Mining and tunnelling | Materials handling | Agriculture |
Recycling | Forestry machinery |
Generators | Rail |
Our solutions include:
Passive systems
Any filter has a finite capacity. Diesel particulate filters must be cleaned out, intermittently or continuously, if they are not to block. This is very important, as an overfilled filter can damage the engine through excessive exhaust backpressure and can itself be damaged or destroyed.
The material trapped in the filter is mostly carbon (C) particles with some absorbed hydrocarbons. There are two principle techniques for removing the particles:
- Combustion with oxygen (O2) - [C] + O2 → CO
- Combustion with nitrogen dioxide (NO2) - [C] + NO2 → CO2 + NO
The merits of the two different techniques can be summarised as follows:
|
O2-based regeneration | NO2-based regeneration |
Temperature required for regeneration | Requires temperatures of around 600°C (or 400°C with a fuel-borne catalyst) | Reaction occurs from 250°C |
Gas used in regeneration reaction | O2 abundant in exhaust gas stream | NO2 needs to be made from NO in exhaust stream. |
NO2-based systems are commonly used because the reaction takes place at temperatures seen in most diesel exhausts. The leading DPF system around the world is Johnson Matthey’s CRT® (Continuously Regenerating Trap) technology, which uses an oxidation catalyst in front of the filter to generate the NO2 required to keep it clean.
DPF systems that are able to regenerate themselves using only the exhaust gas stream, without additional energy inputs, are known as passive systems. The CRT system is able to function in a wider range of conditions than any other passive system and this is the basis of its success. Its advantage is most clearly seen in applications with low exhaust temperatures, an advantage further enhanced in the CCRT system.
Passive systems are favoured, particularly for retrofit applications, because they require no integration with the engine, no source of energy other than the exhaust gases themselves, and no complicated control systems.
Applications with variable or unreliable duty cycles, or with exhaust conditions not suitable for passive systems, require active regeneration. These are discussed in the 'Active systems' section.
Read more on the following passive systems:
Active systems
Any application, in which it cannot be guaranteed that the exhaust gas conditions will be suitable for a passively regenerating system, will require some active regeneration. Even in these cases, it is desirable to maximise the amount of passive regeneration that can be achieved since passive regeneration is 'free', requiring no additional energy.
Almost all active filter regeneration techniques operate by raising the temperature of the filter to around 600°C. This is the temperature at which the particulate (PM) collected in the filter will combust rapidly in oxygen.
Johnson Matthey can supply the following active systems:
- Electrical (DPFi)
- Fuel Borne Catalyst (DPFiS)
- Exchangeable Filter System (DPF-C)
- Burner (DPF-BU)
- Fuel Injection (DPF-RID)
NOx control
NOx (oxides of nitrogen) emissions are associated with smog, acid rain and health risks such as respiratory problems. Johnson Matthey’s SCRT® technology reduces NOx as well as particulates by combining CRT® technology with SCR (selective catalytic reduction).
Nitrogen dioxide, or NO2, emissions are tightly controlled in enclosed spaces, as this is where they can have the greatest effect on people’s respiratory systems. The most effective way of reducing NO2 is to reduce overall NOx at source, for example through the use of an SCRT system. Our Mining-CRT technology can however prevent NO2 increasing at the tailpipe.
Johnson Matthey has developed a passively regenerating DPF system that is suitable for underground mining, as it does not increase NO2 above engine-out levels.
The first part of the unit is the CRT system, designed to reduce CO, HC and PM by more than 90%. This is followed by a decomposition catalyst to bring the NO2 down to the levels required.
Read more:
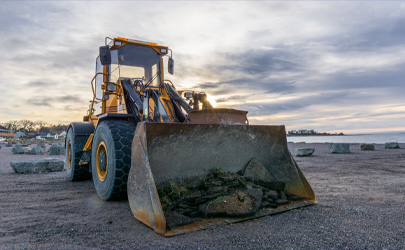