Ready to power the energy transition
Decarbonised ammonia offers a crucial pathway to reducing emissions—providing a versatile future fuel and hydrogen carrier for the energy sector. By leveraging existing infrastructure and supply chains, it plays a key role in enabling the global storage and transportation of low carbon hydrogen.
Building on over two decades of collaboration in ammonia production, Johnson Matthey and uhde® now offer an integrated catalyst and technology solution for producing decarbonised ammonia.
Johnson Matthey’s LCHTM technology integrated with uhde® ammonia process offers a pathway to decarbonise the industry with fully integrated JM and uhde® decarbonised ammonia process, as the solutions to meet the energy transition targets being aimed at globally.
The thyssenKrupp Uhde & Johnson Matthey technology collaboration delivers:
- Generates over $100M value1 over a plant’s life through its excellent energy efficiency and reliability.
- Lowest cost per tonne of ammonia due to optimised solutions1
- Longest plant uptimes on the market with proven ATR burner life of 10 years+
- Catalyst & technology developed together maximising catalyst life
- Joint expertise in delivering the five largest single train ammonia plants in operation globally.
1 value calculated using publicly available data for alternative technologies on a comparative basis of a 3500 tpd production plant over 25 years with costs of natural gas at 4.5$mmbtu and OSBL power at $30/MWh.
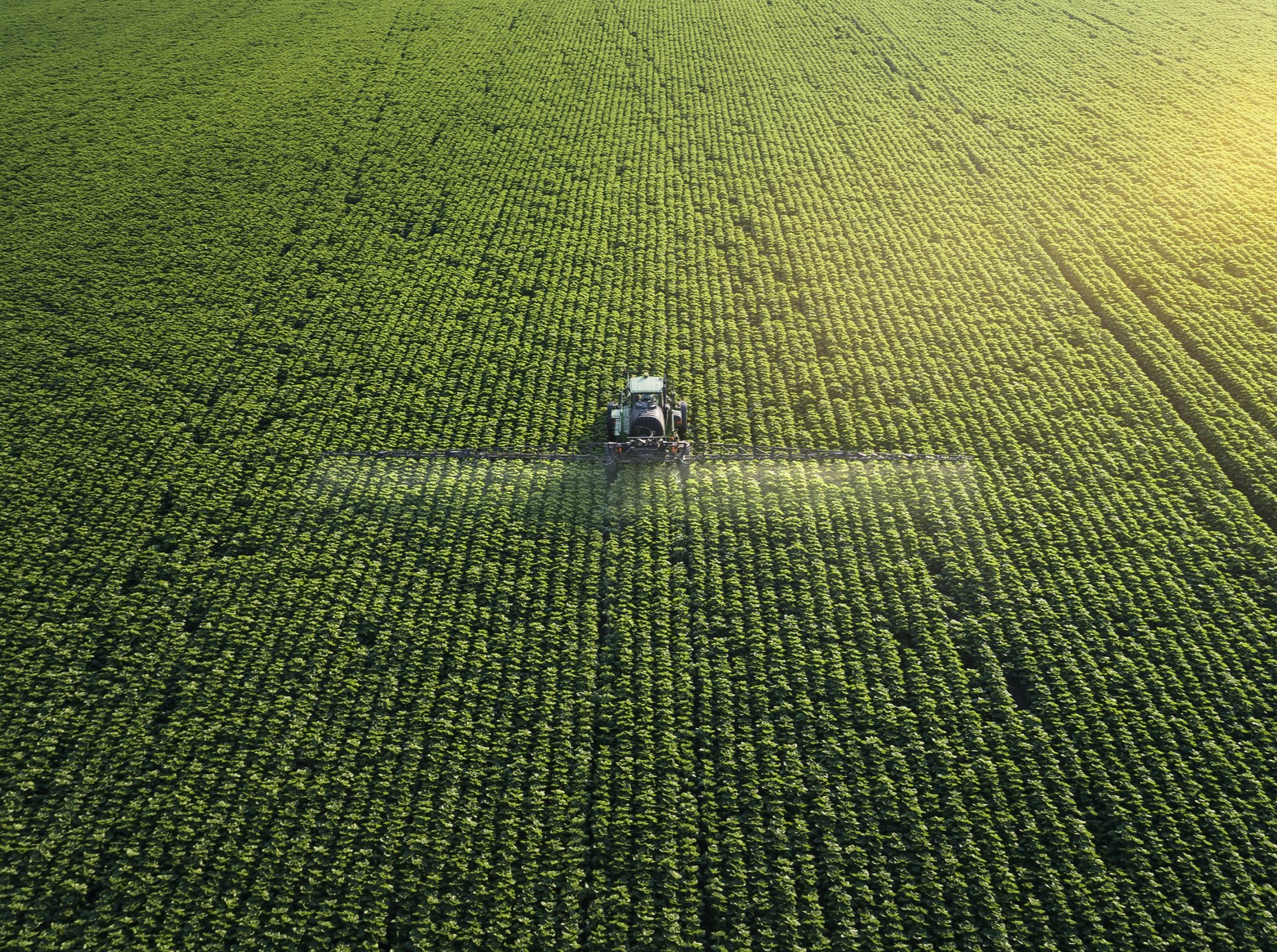
What is decarbonised ammonia?
Decarbonised, or blue ammonia provides an established chemical feedstock that is already in use extensively around the world. As well as decarbonising existing ammonia production for example for use in fertilizers, blue ammonia can serve in the following new applications:
- As a practical hydrogen carrier, facilitating the storage and transportation of hydrogen without the challenges associated with shipping pure hydrogen.
- As a shipping fuel to decarbonise the maritime sector.
- As a fuel for power generation.
By reforming natural gas to produce low carbon hydrogen, it can be efficiently converted into ammonia (NH3) via the Haber Bosch process, resulting in blue ammonia production with significantly reduced carbon emissions.
Demand increase
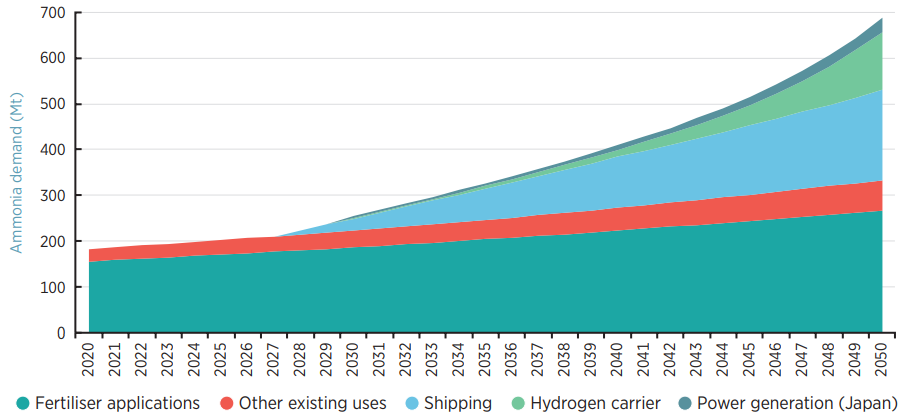
As ammonia's use extends beyond its primary agricultural use, its production is poised to rapidly expand over the next 15 years. Global projections estimate ammonia production will exceed 650 million tons by 2050. For blue ammonia to fulfil its role as a key player in the energy transition, it must be produced where the hydrogen intermediate is generated with high carbon capture rates.
This is best achieved by using advanced reforming technology, like our LCH technology flowsheet, which employs our autothermal reforming (ATR) process.
The advantage of this approach is that it keeps all the CO2 under process conditions, at pressure, and in a concentrated form, supporting efficient capture using proven technologies. Our ATR features a unique long neck, single nozzle design that means robust operation and long, efficient operating cycles, perfectly aligning with the demands of the ammonia industry. Explore our flowsheet that offers an efficient process able to supply low carbon hydrogen delivering up to 99% carbon capture efficiency to support sustainable ammonia production.
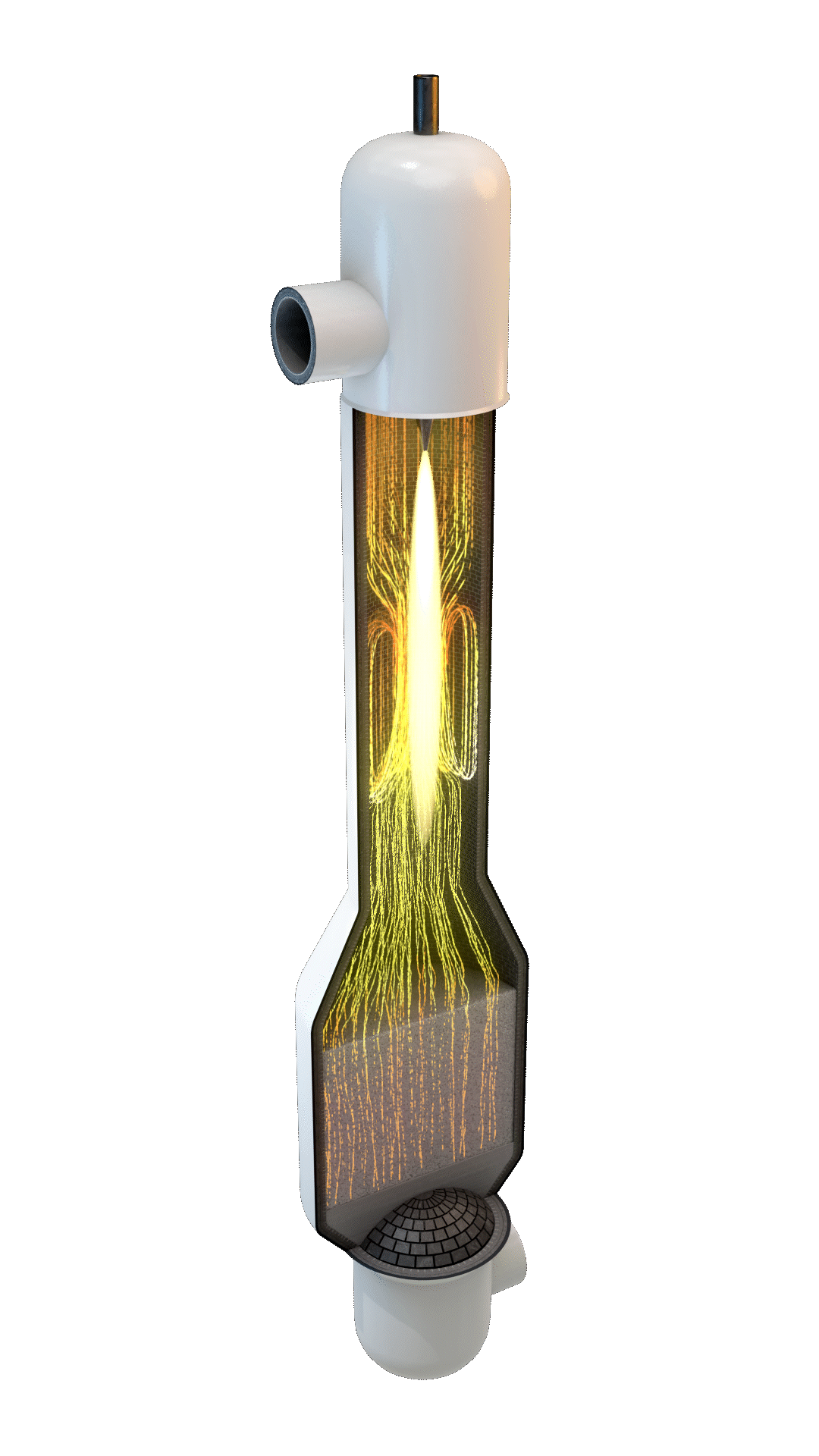
LCH technology to ammonia: Secure your future with advanced decarbonised ammonia production technology
Applying 60 years of syngas value chain leadership, our integrated decarbonised ammonia production solutions offer customers the flexibility of two proven flowsheets.
Our flowsheets offer JM’s award-winning LCH technology, which utilises our ATR with a fully integrated steam system. This setup maximizes the value captured from the gas by efficiently using it alongside the steam system, which extracts hydrogen from water splitting and provides cost-effective motive power to the flowsheet. This proven configuration ensures superior efficiency, cost-effectiveness, and high carbon capture rate performance, making it ideal for decarbonised ammonia production. Alternatively, ATR can be combined with our GHR, which reduces the gas requirement per tonne of product and uses green power instead of steam to power drives across the flowsheet.
Explore processes for decarbonised ammonia production
LCH technology ATR flowsheet with ammonia loop integration
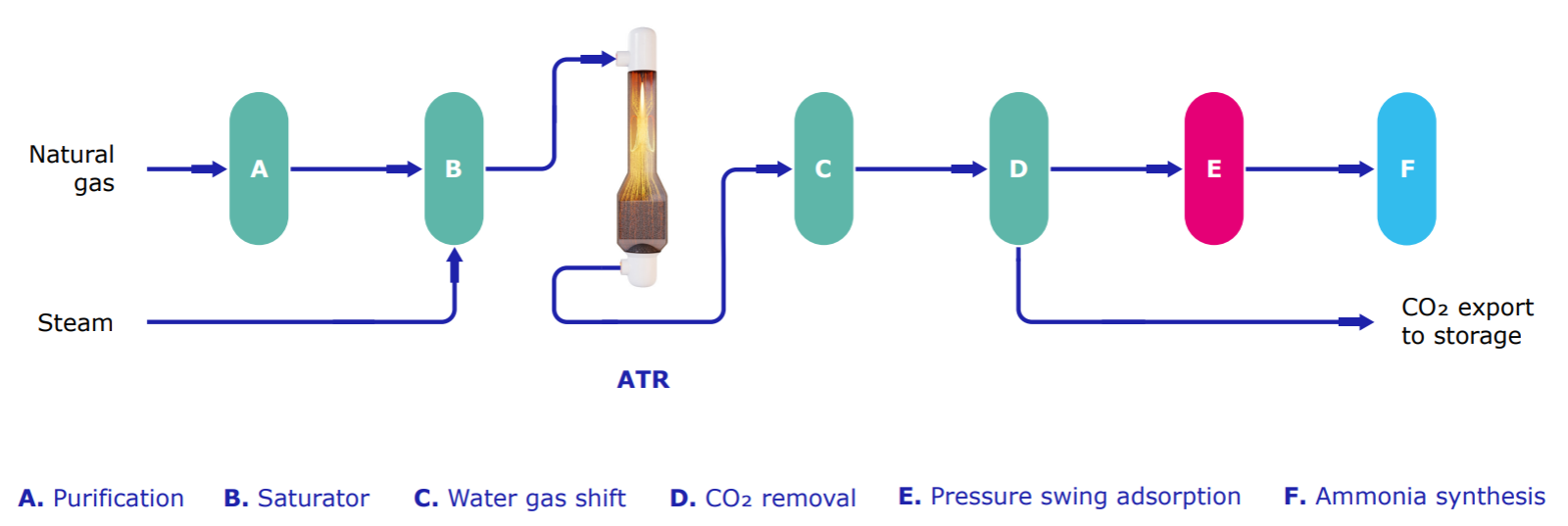
Key features:
- Fully integrated high-pressure steam system
- Low methane slip throughout the cycle
- Unique "long neck" design for maximised throughput and uptime
- High velocity for better feed and oxygen mixing
- Uniform temperature control to protect catalysts
Our alternative flowsheet offers the option to reduce the reliance on gas and increase the use of outside battery limit power (ISBL) taking the energy created from the ATR process and using it to drive further hydrogen production in our GHR (Gas Heated Reformer). This flowsheet significantly reduces the gas requirement to make the same level ammonia, and where green electrical power is available, it also reduces its carbon intensity.
LCH technology GHR + ATR flowsheet with ammonia loop integration
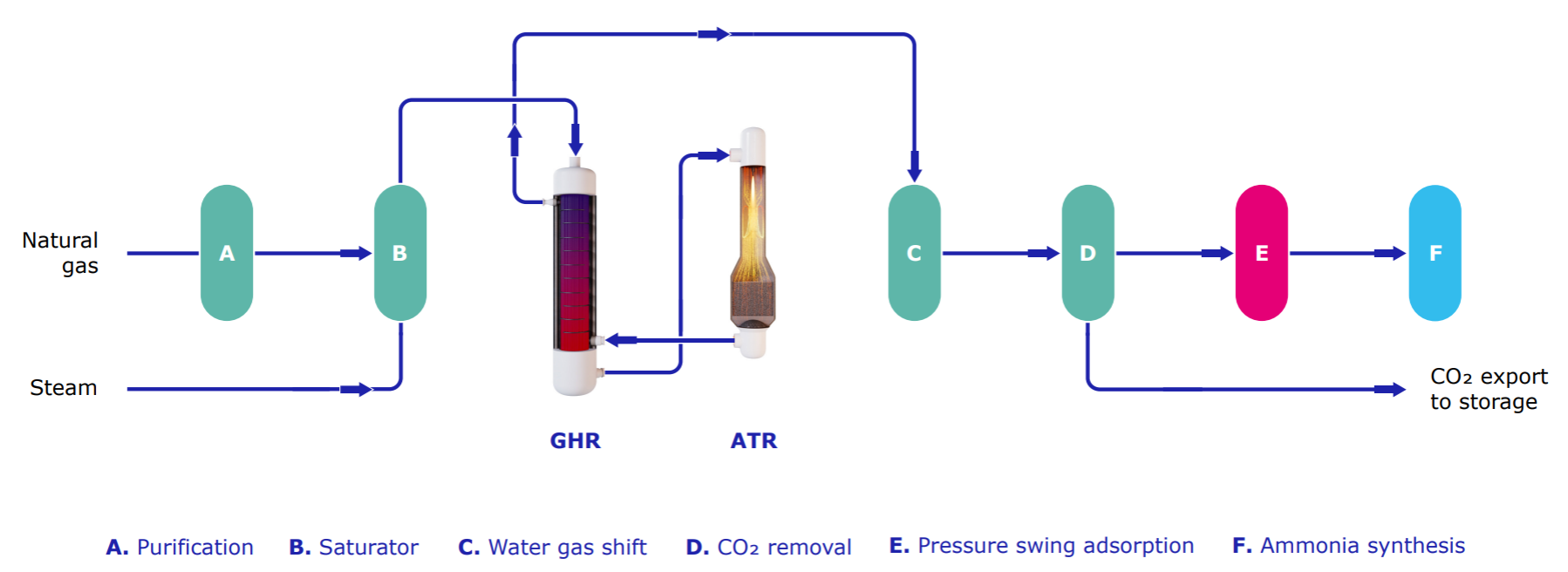
Our unique GHR + ATR flowsheet integrates leading hydrogen and ammonia technology, offering the lowest carbon intensity in the market. It also provides the option to decouple ammonia and hydrogen production.
GHR + ATR flowsheet key features:
- Highest feedstock efficiency for ammonia production
- Lowest carbon intensity available, decreasing with the electricity grid
- Options to decouple ammonia and hydrogen
- Decoupled steam systems for outside battery limit (OSBL) power
Choose our leading blue ammonia solutions to achieve exceptional efficiency, cost-effectiveness, and minimal carbon intensity, ensuring your success in the evolving energy landscape.
Decarbonised ammonia production: Ready now, fit for the future
JM is proud to be at the heart of the transition towards a low-carbon global energy mix. Our decades of syngas leadership, combined with next-generation LCH technology, provide our customers with the solutions to get ahead and stay ahead in the rapidly evolving energy and fuel markets.
Discover our recently announced projects to discover how we’re powering the hydrogen economy with LCH technology for hydrogen production:
Confidential, North America
- BEP Complete, FEED in progress
- Start-up estimated: 2029
- >1 GW for refinery and local industry uses
Confidential, Europe
- BEP in progress, FEED in progress
- Start-up estimated: 2028
- 1 GW for industrial decarbonisation
HyNet, Vertex and Essar Stanlow, UK: LCH (GHR+ATR)
- BEP complete, FEED complete
- Start-up estimated: 2026
- 350 MW for refinery and local industry users
H2H Saltend, Equinor and Linde Saltend, UK (GHR+ATR)
- BEP in progress, FEED in progress
- Start-up estimated: 2028
- 600 MW for local industry power generation
Kellas Midstream H2NorthEast, Teesside, UK: LCH (GHR+ATR)
- BEP in progress, FEED in progress
- Start-up estimated: 2029
- 355 MW for local industry users
bp H2Teesside, Teesside, UK: LCH (GHR+ATR)
- BEP in progress, FEED in progress
- Start-up estimated: 2028
- 1.2 GW for refinery and local industry users
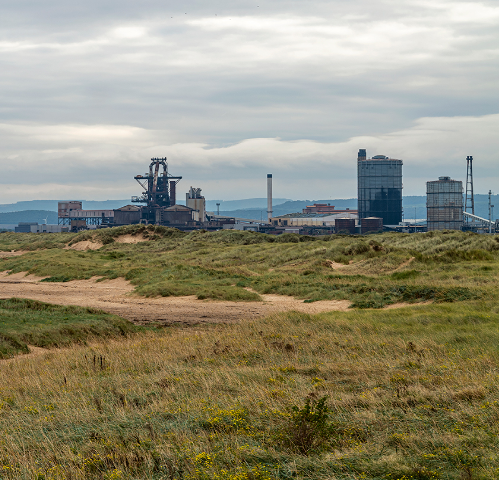
Ammonia plant performance
Johnson Matthey offers world class catalysts, absorbents and services for ammonia production. Our focus is delivering the best plant performance in the world. We have ongoing development programmes producing new and better catalysts and improving the process technology for the ammonia industry.
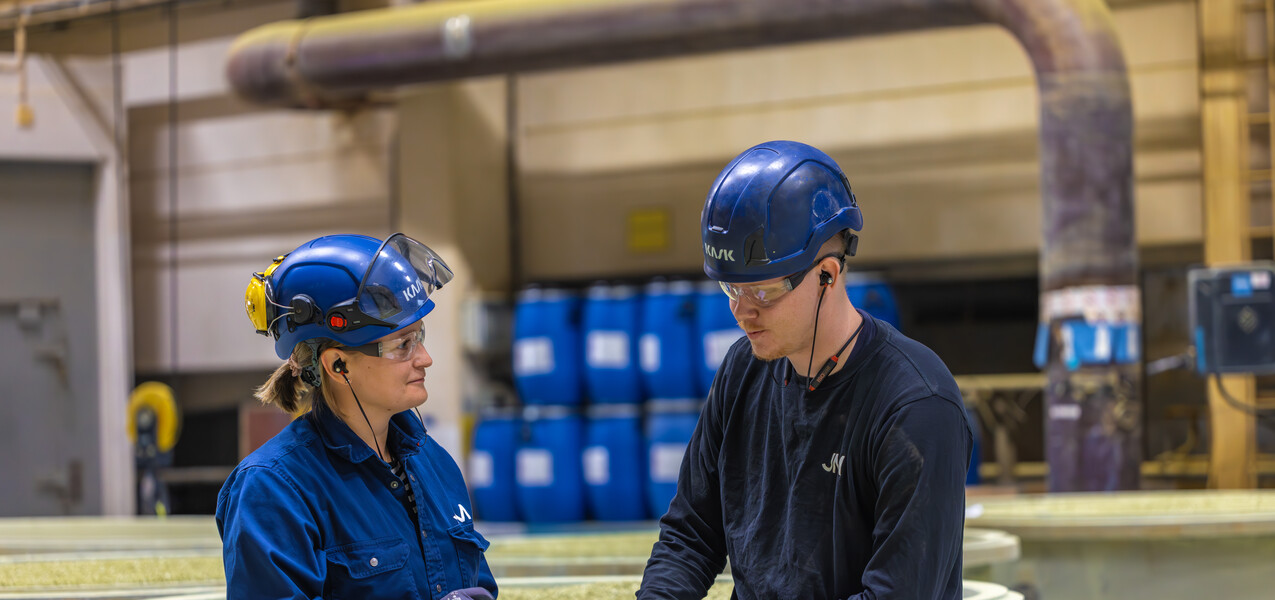