Powering the transition to net zero
In the shift to a more sustainable future, sectors such as transport, energy and the chemicals industry are experiencing major transitions. Consumers are pushing for sustainable energy solutions, and governments are making ambitious commitments to tackle climate change and reach net zero.
Electrolytic (green) hydrogen is a truly carbon neutral solution that will play a significant role in enabling the transition to net zero, most significantly in hard to decarbonise areas, such as transport, steel, and chemical industries. It uses renewable energy sources, such as wind or solar power, to split water into oxygen and hydrogen using electrolysis, without releasing harmful emissions or particulates.
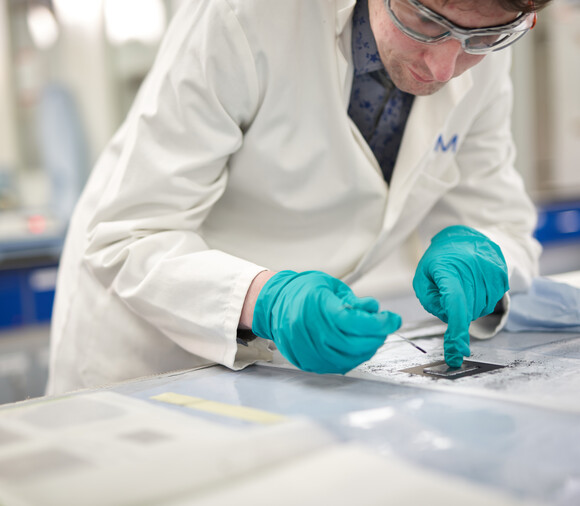
Although green hydrogen is today more expensive to produce than conventional (grey) or CCS-enabled (blue) hydrogen today, the key input - renewable energy - is both increasing in capacity and reducing in cost. And as the cost of electrolysers continues to fall with continued innovation, increased capacity, and supply chain development it is beyond doubt is that electrolytic hydrogen will play key role in the transition to net zero.
Here to power your progress
At the heart of the electrolyser sits the catalyst coated membrane (CCM). At JM we are focused on the development and large scale manufacture of high performance CCMs. Our deep roots in the development of catalytic coatings, PGM (platinum group metal) science and fuel cell technology enables us to lead the way in the development and manufacture of these technologies for a range of applications, offering next generation performance whilst driving down cost.
The demand for continuous development in how we produce and store clean energy is clear, and spans multiple industries and applications. We continue to invest in our technical capabilities and our manufacturing assets, leveraging expertise developed in our fuel cell component manufacturing business. With manufacturing sites in the UK and significant expansion planned across North America, UK, and China our teams are ready to work alongside you in your journey towards a production ready electrolyser system.
Positioned to deliver
As the only CCM supplier with in-house catalyst and membrane technologies, we are uniquely positioned, securing supply chains of critical raw materials and scaling rapidly. We leverage our position in the value chain by harnessing the potential of each CCM layer, balancing the technical trade offs that exist, to support customers in achieving targets on performance, durability, and cost. And as the needs of our customers evolve, so do we. We’ll continue to invest in capacity and R&D so we can stay ahead of the curve and meet the demands of the future.
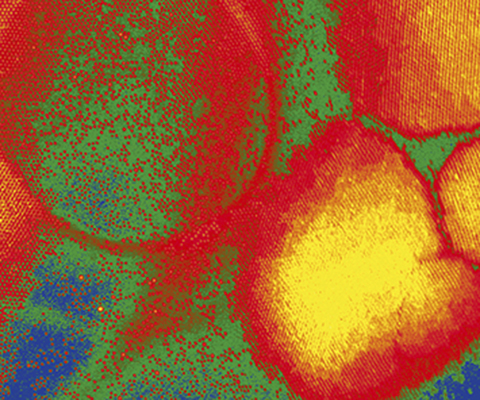
Responsible growth
We are the largest secondary platinum group metals (PGM) refiner and recycler in the world. Our products contain on average 70% recycled PGM content, supporting customers in their sustainability goals and a achieving a lower carbon footprint.
While our products help deliver our vision for a cleaner, healthier world, we also manufacture them in ways that lower our own environmental impact. That is why we have embedded sustainability in everything we do and are committed to minimising our environmental footprint. We’ve also committed to net zero by 2040 for our operations.
Not just a product; a partnership
Our success in developing customer solutions is built on strong partnerships and collaboration.
Understanding your systems, challenges and vision for sustainable growth is a vital part of the process. We work together with you at every step of the way to ensure we’re in tune with the fine detail of what makes your business model work. It's this close relationship that helps us deliver innovative products tailored to meet your performance, cost, safety, and durability requirements.
By partnering with us, you can leverage our world class science and experience to achieve tailored electrolysis products for the applications you are developing. We can also scale products to meet the demand for rapidly growing markets, providing you with competitive products at commercial scale.
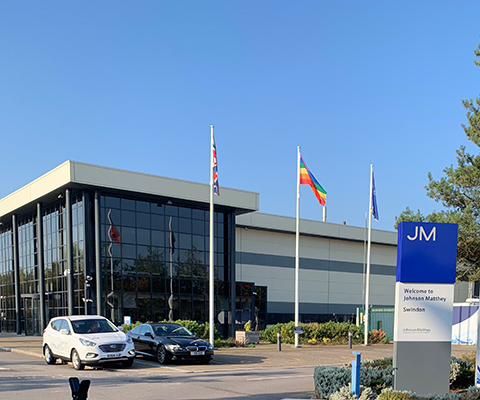