Electrolyser technologies: do we need a winner?
There’s more than one way to make electrolytic (green) hydrogen, but is there a right way? Eugene McKenna, JM’s Commercial and Strategy Director, reviews current electrolyser technologies.
17 February 2023
The importance of hydrogen in the race to net zero cannot be overstated. As an energy carrier, it is able to decarbonise sectors that electricity cannot, producing no carbon emissions when it’s combusted in an engine or used in a fuel cell. Plus, it can be made by electrolysis – the process of using electricity from sustainable sources to split water into its components: hydrogen and oxygen.
No wonder, then, that hydrogen is often called the ‘fuel of the future’.
And hydrogen’s future is getting closer and closer. International markets are expanding rapidly and incentives, such as the US Inflation Reduction Act, are only accelerating this growth. Investment plans of key players in the hydrogen value chain, such as Johnson Matthey, Plug Power and Enapter, have gathered momentum, incentivised by these favourable economic tailwinds.
For every kilogram of hydrogen produced (with a carbon footprint of less than 0.45kg CO2 equivalent) the Inflation Reduction Act promises tax credits of $3. It’s hoped such measures could increase electrolytic (green) hydrogen capacity by an additional 20MT to 30MT by 2030 to 2035.
Trade-offs in the technology tool kit
Although water electrolysis can be more expensive than other hydrogen production routes today, depending on the cost of natural gas versus that of renewable electricity, it is one of only a handful of non-fossil fuel options and the key input – renewable energy – is both increasing in capacity and reducing in cost. The challenge for industry is to be ready to keep pace and deliver affordable, reliable electrolytic hydrogen into the supply chain when renewable energy sources are in place to meet demand.
There are four main electrolyser technology types, distinguished based on the nature of the electrolyte which is used and the temperature of operation:
Technology | Electrolyte | Temperature of operation |
Liquid alkaline (AEL) | Liquid potassium hydroxide | Low |
Proton exchange membrane (PEM) | Solid polymer electrolyte in water | Low |
Anion exchange membrane (AEM) | Solid polymer electrolyte in potassium hydroxide | Low |
Solid oxide (SOEC) | Solid ceramic electrolyte | High |
Each technology is at a different stage of maturity and offers its own advantages and disadvantages. As such, when designing a hydrogen production system, three main trade-offs need to be considered and balanced to determine which technology is best suited to the application: efficiency, system cost (CapEx and OpEx) and lifetime.
A critical balancing act
Energy consumption and how efficiently this is turned into hydrogen is a major consideration – most electrolyser types would be considered similar in terms of overall efficiency, but they differ in their ability to cope with the intermittent nature of renewable energy. This is an important factor because the sun doesn’t always shine, and the wind doesn’t always blow.
Overall cost of the electrolyser system is impacted by many factors, for example:
- The time taken to start up a system ‘from cold’ which directly contributes to a systems operating cost. AEL technology doesn’t perform so well in this respect and so is best suited for direct connection to the grid, whereas PEM electrolysis, with its fast response time, is perfect for connection to renewable electricity.
- As the most mature technology, AEL is furthest down the cost curve, but the other technologies are maturing and catching up. Plant footprint, dependant on rate of hydrogen production per area, is a key cost consideration, especially where land area is limited. Here, boasting the smallest footprint, PEM is ideal for smaller installations.
- System complexity can also impact system cost. Some electrode materials cost more than others, and corrosive chemicals in the electrolyte solution often require more robust system components and more regular maintenance. AEM technology is expected to have the lowest capital cost in the long-term, with lower concentrations of corrosive chemicals than AEL technology and less costly electrode materials than PEM technology.
Durability is the third major consideration. Here the most proven technology is AEL; the technology already having reached maturity. However, other technology types, particularly PEM with no corrosive chemicals in the electrolyser system, are increasingly demonstrating the durability of their systems at multi megawatt scale.
A SOEC electrolyser has a ‘similar-but-different’ consideration: this technology needs to operate at temperatures high enough for the solid oxide electrolyser to function properly, which is about 700-800°C. Furthermore, the reaction uses a considerable amount of heat supplied at this temperature as well as electricity and it is important that the source of this heat is renewable, if the hydrogen produced is to be low carbon. In comparison, AEL, PEM and AEM all operate at just 50-90°C. But in the cases where waste heat is available, such as in chemical production processes and steel making, the pay-off may make sense since it typically results in high efficiencies – close to 100%. Heat at 800°C is rarely waste however as it can be put to many uses.
The paradox of choice
For some applications, the technology choice is relatively straightforward. For example, in applications where excess high-quality heat is generated by other processes (especially if the source of that energy is renewable), SOEC may be favoured. However, for applications where multiple technologies offer a benefit, the decision can be complex and will depend on balancing the trade-offs that exist.
For example, optimising for efficiency with intermittent renewable electricity favours a plant designed using PEM technology, with a small footprint, less complex system but (in the short-term) higher system cost. Focussing on proven durability or a low-cost system means using AEL, resulting in a larger footprint, more complex system and efficiency losses when connected to intermittent energy supply. But in the longer-term, AEM technology is forecast to be lower cost than PEM with a less complex system than AEL, once sufficient durability has been proven. It will however have a larger footprint than PEM.
Therefore, it’s important in the race for net zero for the electrolyser technology race not to have one winner. It’s beneficial to develop different technologies in parallel to cater to the broad range of applications that are in the pipeline now and those that will emerge, so project developers continue to have multiple systems to choose from. As the hydrogen market scales up, we’ll need a diverse network of hydrogen producers around the world, each using the right technology for them, to meet demand and weather the ups and downs of market movements.
At Johnson Matthey, we’re partnering with other industry leaders, like Plug Power and Enapter, who specialise in different technology areas across the electrolyser value chain. It’s a strategy that enables each partner to focus on what they do best, so we can work to develop the global hydrogen economy, at pace, together, and turn the fuel of the future into a technology of today.
Read more
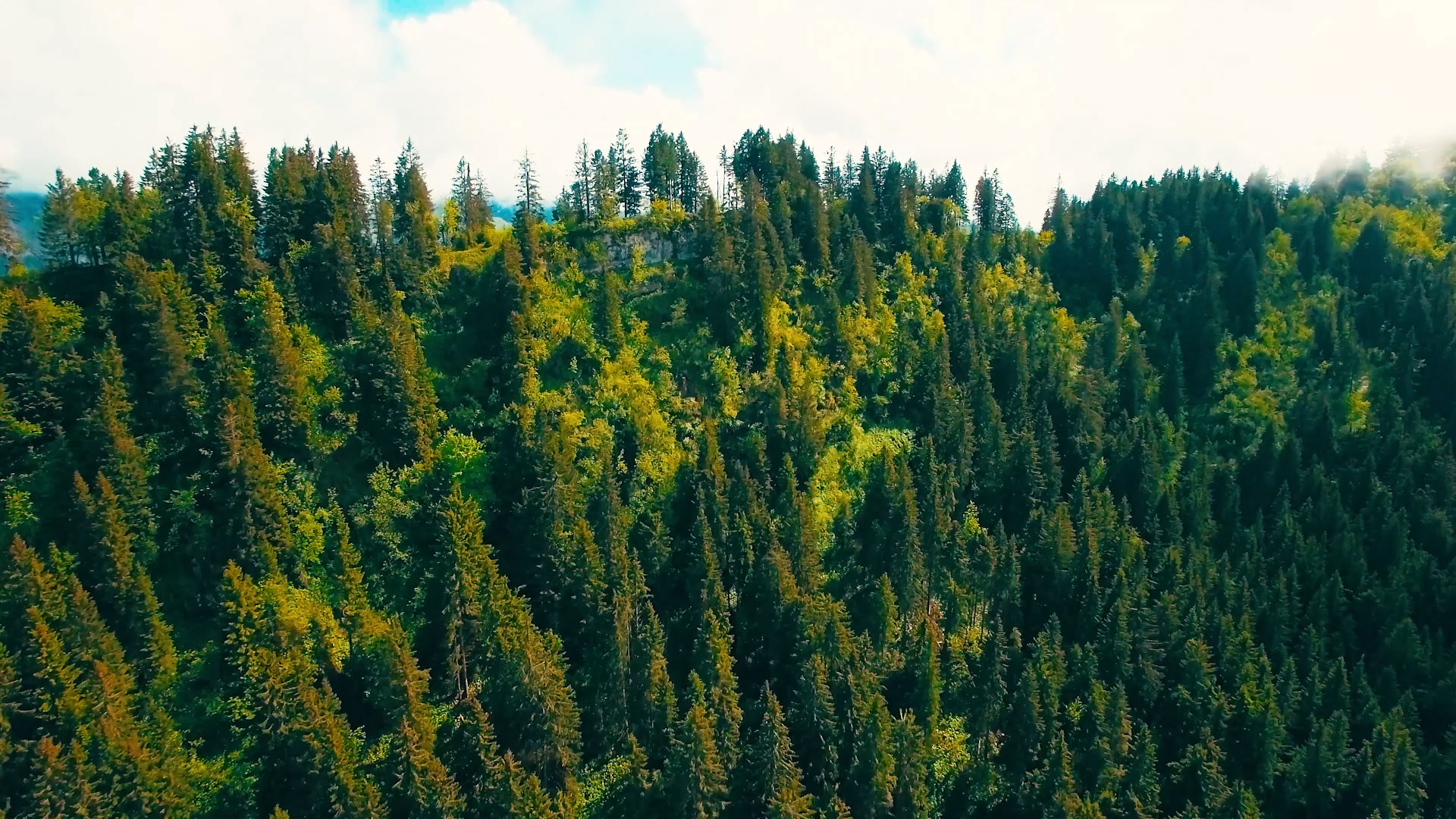