Our recycling and circular solutions underpin every aspect of our business. By conserving and recycling these critical materials to enable their circular use, we’re helping make the world more sustainable. We’ve developed highly advanced processes for extracting and separating platinum group metals (PGMs) from complex materials, and with our technical support teams we work with our customers to optimise precious metals recovery. We’re experienced in handling highly valuable materials, with leading security standards and end to end control of the metal.
PGM refining
With our refineries in Europe, US and China, and through our global refining network of partners, we offer full geographic coverage and complete refining solutions. Along with our full refine-supply cycle, we’re one of the only companies capable of refining all seven precious metals, helping you to efficiently recover:
-
Platinum
-
Palladium
-
Rhodium
-
Iridium
-
Ruthenium
-
Gold
-
Silver
Practising a deep understanding of material and analytical science, pyrometallurgy and multi-stage chemical separation, we have powerful capabilities to refine a broad spectrum of complex materials.
From spent catalysts and chemical residues to electronics and jewellery scrap, our capabilities span across a variety of industries; explore our matrix for an extensive list of materials we refine.
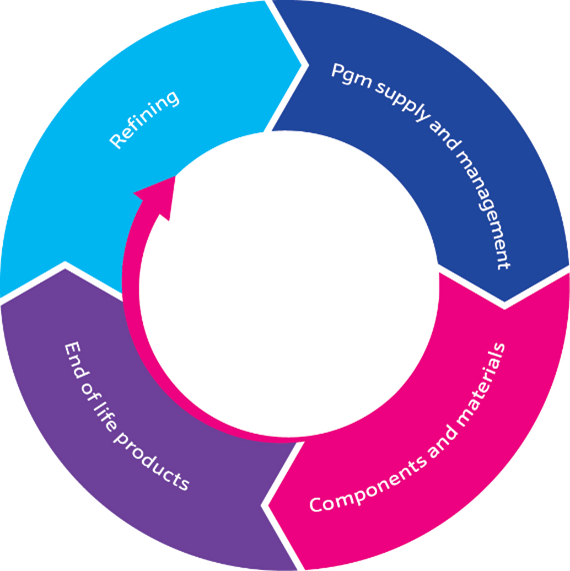
Fuel cell and electrolyser recycling
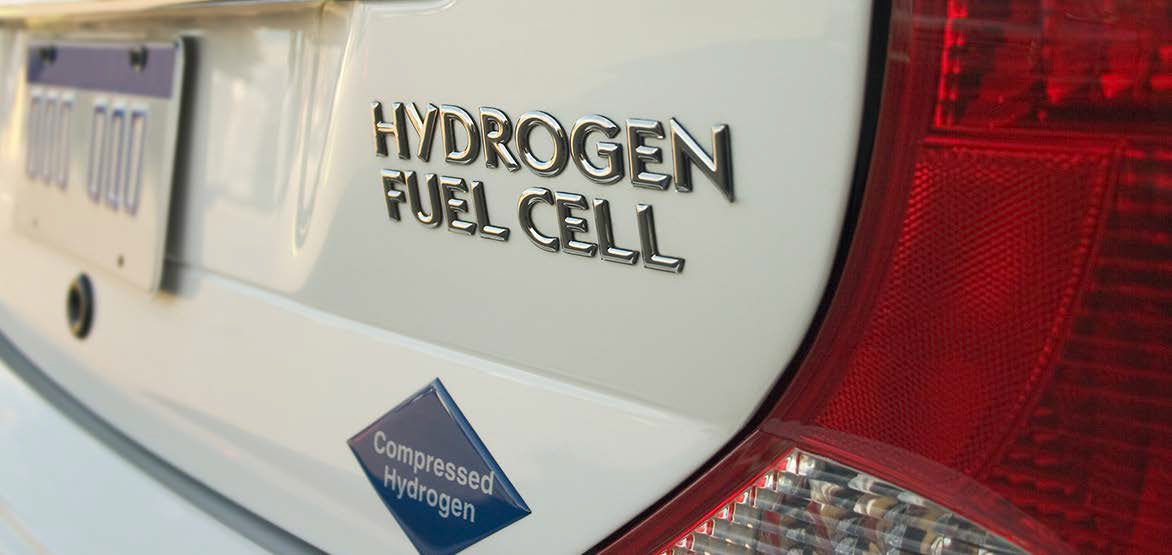
PGM recycling and refining stages
Our refining process allows us to efficiently and securely extract and recover PGMs from complex products, and then refine them to commercial grade purity. From initial material analysis to comprehensive metal management services, we guide and advise you at each step of the process.
Our process involves up to four key stages, using a combination of pyrometallurgical and chemical treatment processes.
Material can enter our refining circuit at different stages depending on its composition, helping to optimise the process.
The four refining stages
Evaluation
Evaluation is a critical stage, in which we determine the PGM content of the material and how long it will take to refine. We do this through assaying, and our processes are widely trusted and proven; it’s what we’ve been doing for over 200 years. Our industry leading standards are recognised through our global accreditation.
Our experienced chemists ensure a high level of accuracy in our assay process, using advanced sampling methods and wide-ranging analytical techniques that are optimised for each material. They study the total matrix of the material by evaluating both precious metal and non-precious metal content. This analysis allows us to determine the best processing route for each material, so we can offer our customers the most competitive refining option.
Material tracking is crucial during this stage; on receipt all customer batches are uniquely barcoded to ensure full traceability during evaluation.
Smelting
Chemical leaching
Chemical separation
Precious metals management
Our team of PGM market experts provide comprehensive support in metal management: from developing customers’ metal strategy, to advice on deploying refining outturns to fund future products requirements. Our metal trading and management services give customers the freedom to choose metal return options, up-to-date metal trading information and help in understanding how the PGM markets are likely to develop.
For more information visit our precious metals management pages.
Webinar - Platinum group metals: The champions of circularity
Watch the circularity webinar
Webinar: Platinum Group Metals - The champions of circularity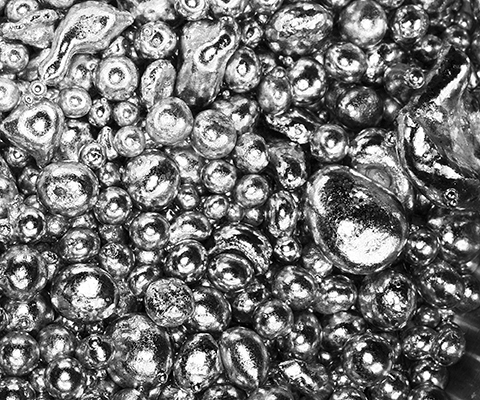
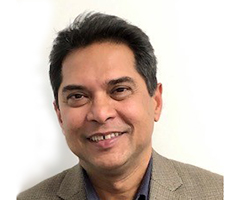
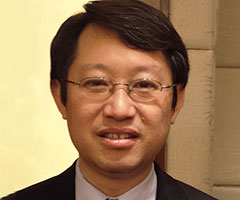
Secondary supplies and recycling
Learn more about the importance of secondary supplies and recycling
Read More
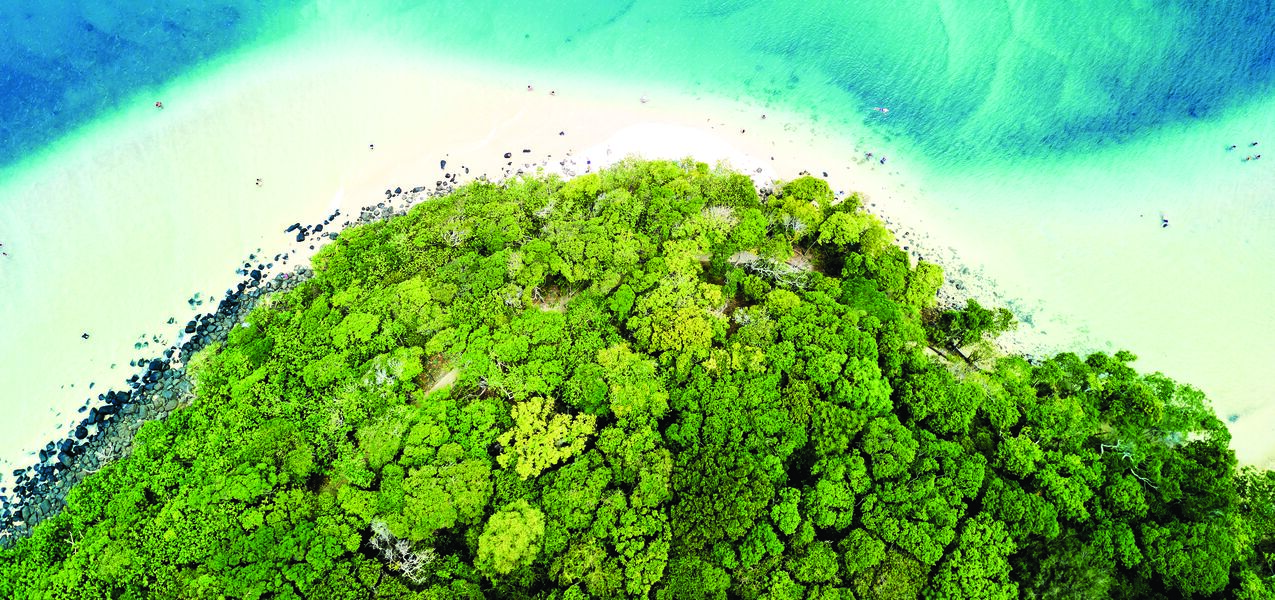