Autothermal reforming catalysts
Autothermal reforming (ATR) increases the conversion of methane to hydrogen and, in an ammonia process, adds nitrogen to the process by introducing air. The mechanical and physical requirements of an autothermal reformer are the most demanding in the plant.
Johnson Matthey combines advanced computational fluid dynamic (CFD) techniques and process modelling, calibrated with data from our reforming pilot plant, to ensure the best performance from our state of the art range of authothermal reforming catalysts.
Our portfolio includes specialised products such as KATALCO™ 89-6Q and KATALCO 89-9Q, specifically designed for use in the top of the autothermal reformer where both temperature and steam partial pressures are high. Normally, this combination can lead to fast volatilisation of alumina in conventional catalysts, triggering process gas maldistribution issues within the bed and degredation of downstream equipment. However, our catalyst can ensure high activity and long-term stability in your autothermal reformer.
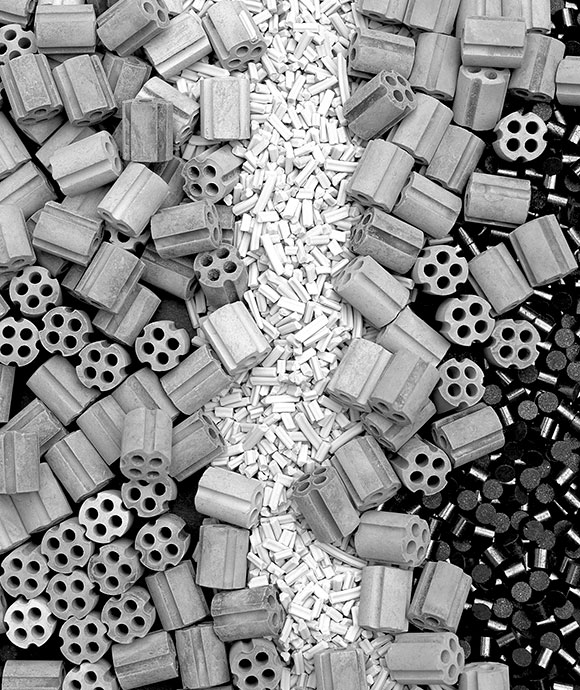
Autothermal reforming in ammonia plants
For ammonia plants, we use our combined knowledge of process technologies and catalysis to maximise the efficiency of autothermal reforming operations.
The design of the burner in the autothermal reformer used to distribute the air is an important factor in the performance of the unit. We have developed designs to offer efficient and reliable burners in either single or double ring configuration depending on the needs of the plant and the result is an optimised, bespoke engineering piece of equipment which creates the most suitable conditions for catalyst operation
LEARN MORE ABOUT OUR ATR CAPABILITIES
KATALCO QUADRALOBE autothermal reforming catalysts
JM’s range of KATALCO QUADRALOBE™ autothermal reforming catalysts provide high stability and high activity, offering the best mix of activity, pressure drop and high temperature stability for your application.
Catalysts available in this range:
- KATALCO 23-8Q
- KATALCO 28-4Q
- KATALCO 54-8Q
- KATALCO 54-9Q
- KATALCO 89-6Q
- KATALCO 89-9Q