Addition systems
INTERCAT™ addition systems have been widely used in the FCC (fluid catalytic cracking) process since the mid-1980s; today there are over 300 units installed in refineries throughout the world. Without continuous catalyst addition and dedicated addition system, the FCC unit cannot operate or perform its essential functions. Additives are also used to enhance profitability or comply with environmental regulations in the FCC process.
DOWNLOAD A NOVEL APPROACH TO FCC CATALYST WITHDRAWALS
DOWNLOAD FCC FLEXIBILITY THROUGH ADDITION SYSTEMS
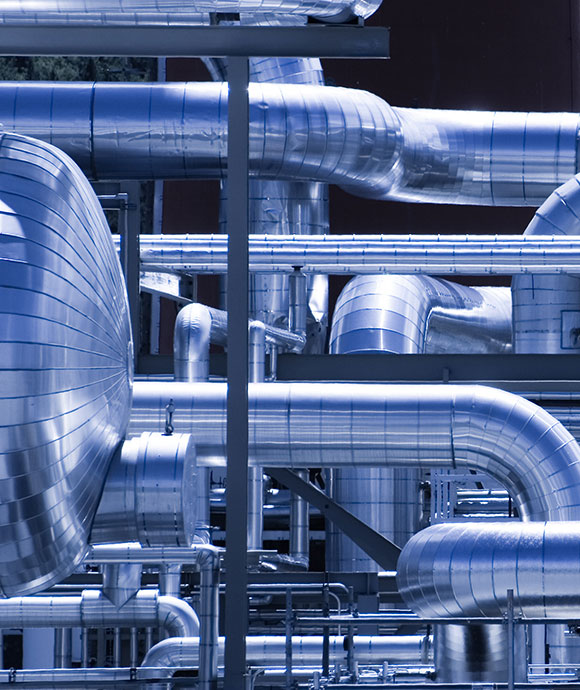
Addition systems for all catalyst injection needs
Addition systems come in a variety of configurations fit for users’ needs, from the injection of a few kilograms of additives per day to tens of tons of fresh catalyst per day.
The standard INTERCAT addition system consists of a storage vessel for the additive or catalyst, associated piping and equipment to load the vessel and a control system which feeds the supply of catalyst to the FCC unit.
Johnson Matthey also offers the specialized MSCAS (Multi-source catalyst addition system), that can add catalyst or additive from up to 4 different sources, such as hoppers or totes.
The advantages of an INTERCAT addition system include:
- Reliable and precise additions. Allows for improved control of unit severity.
- The ability to control e-cat activity. Permits higher throughputs, higher severities or the processing of a greater range of feedstocks.
- The ability to add additives separately to the fresh catalyst. Allows the refiner the flexibility to quickly respond to changing market conditions.
- More stable and efficient FCC operation. Adding small shots of additive over a 24-hour period is up to three times more efficient than adding large quantities at the end of each shift.
All INTERCAT addition systems are designed and supported internally by Johnson Matthey engineers and technicians. This allows for fast troubleshooting by those directly involved with the loader if issues do arise.
Click for in-depth details and technical specifications
Standard design
For the standard loaders, the main vessel is mounted on 3 load cells for highly accurate weight measurement and addition. The vessel’s outlet line is equipped with a single valve to control the flow of catalyst to the FCC. This specially designed valve is the only moving part of the system in frequent contact with the catalyst during normal operation, maximising reliability. The system is controlled by an INTERCAT Management System (IMS) Controller which allows for operation locally or through the refinery’s DCS system.
The design and control logic of the Johnson Matthey system ensures extremely accurate catalyst additions at regular intervals throughout the day. The logic for the controller was developed internally based on years of operating experience.
The addition systems can be set up to manually refill from totes, flex hoppers, bags, or existing refinery hoppers. The addition system can also include auto-refill capability from these same sources for ease of operation.
The system also includes a Sintered Metal Filter to control particulate emissions. It combines high permeability, efficiency of particulate capture, and automatic self-cleaning.
Digitalisation solution
To simplify additive and catalyst inventory management and save valuable supervisory resources, Johnson Matthey patented AIM TECHNOLOGY™ - its Automatic Inventory Management system. The system tracks additions, the onsite inventory of FCC catalyst and additives as well as facilitates remote monitoring for troubleshooting and diagnosis purposes, making AIM TECHNOLOGY an excellent digitalisation solution.
Addition system sizes and designs
- Single Additive or Catalyst Addition System (AAS), usually 1 to 10t capacity.
- Fresh Catalyst Addition System (CAS), up to 120t capacity or 4t day hopper design.
- Multi-Compartment Addition System (MC3), containing three separate compartments.
- Multi-Source Catalyst Addition System (MSCAS), a skid mounted unit that can draw catalyst and additives from up to 4 separate hoppers or tote bins.
- COP Mini Loader, designed to add shots as small as 0.1 kgs/day to accurately spread promoter addition throughout the day to improve after burn and CO control.
INTERCAT Catalyst Withdrawal System
In the Johnson Matthey Catalyst Withdrawal System, hot spent catalyst is withdrawn continuously into a collection vessel which is very similar to a 200 ft3 addition system on load cells. The rate of catalyst withdrawal is dynamically controlled using vessel weight readings and differential pressure control. When the vessel is full, the catalyst is automatically transferred to the spent catalyst hopper. The skid contains a specially designed heat exchange module allowing the withdrawn catalyst to be cooled to a specified temperature.
Gases vent from the collection vessel through a Sintered Metal Filter (SMF) and the vessel pressure is regulated by a valve on the clean side of SMF thus eliminating erosion.
Most existing FCC Catalyst Withdrawal Systems are very basic with simple manual control by gate valve and manual carrier air adjustment. High temperatures and poor velocity control result in high erosion rates of valves and lines resulting in frequent maintenance being required with the subsequent risk of hot catalyst spills. Erosion of the throttling device for controlling withdrawal rate is completely eliminated with the Johnson Matthey Catalyst Withdrawal System by a pressure balance design.
Infrequent withdrawals also result in large, sudden changes in regenerator catalyst bed level which can have a significant impact on unit operation and flue gas emissions. With the Johnson Matthey Catalyst Withdrawal System, withdrawal is continuous so bed level can be kept constant.
There are multiple Johnson Matthey’s Catalyst Withdrawal Systems installed globally, on two continents.
Fabrication certification and qualifications
Johnson Matthey has the ability to manufacture addition systems to multiple National Standards, including:
- The National Board of Boiler Pressure Vessels (NB) Stamp.
- The National Board of Boiler Pressure Vessels (R) Stamp.
- The American Society of Mechanical Engineers (U) Stamp.
- PED: Johnson Matthey Process Technologies are qualified to build pressure vessels in accordance with The European Community Pressure Equipment Directive 97/23/EC.
- Canadian Certification (CRN).
Standard control systems are supplied with Zone 2 (Class 1, Div 2) certification.